新闻中心
氧化锆珠尺寸研磨时间对油墨分散性的影响
作者:admin日期:2020-01-22阅读 553
UV喷墨油墨对分散性要求很高,而研磨条件对油墨的分散性有很大的影响。为了获得分散性良好的UV喷墨油墨,在固定油墨的条件下,通过改变研磨时研磨珠的大小、以及将不同大小的研磨珠以一定比例混合研磨油墨,测试不同研磨时间获得的油墨粒径大小分布,从而考察研磨珠的大小以及研磨时间对油墨分散性的影响。
实验结果表明:研磨珠越小,研磨效果越好,直径为1.0~1.2mm的研磨珠研磨得到的油墨,95%的粒径在0.972μm
以下;在佳研磨时间下才能获得分散性良好的油墨,且不同大小研磨珠的佳研磨时间不同,直径为2.0~2.2mm、1.6~1.8mm、1.0~1.2mm的研磨珠对应的佳研磨时间分别为105min、105min、90min;中小珠混合比为1∶1研磨得到的油墨的分散性好,油墨90%的粒径在0.656μm以下。
随着数字技术在打印及印刷行业的广泛应用,喷墨技术得到了迅速发展。喷墨印刷使用的呈色材料(喷墨油墨)有水性油墨、溶剂型油墨和UV油墨。UV喷墨油墨具有印刷质量高、节能、、瞬时干燥、承印物使用范围广、固化前不会因干燥而堵塞喷头、油墨成分稳定等优点,具有巨大的发展前景和市场潜力[1]。UV喷墨油墨由颜料、预聚物、单体及各种添加剂组成,颜料颗粒大小及在油墨体系中的分散状态直接决定着UV喷墨油墨能否顺利从喷嘴喷射,且颜料的分散性对油墨的着色力、透明度等性能有较大影响[2]。因此,确定颜料分散工艺技术条件是开发、制备UV喷墨油墨必须解决的技术问题。
一般来说,UV喷墨油墨属于黏度油墨,通常使用研磨分散方法进行制备生产。在研磨分散过程中,研磨介质(氧化锆珠或玻璃珠)的大小及用量、研磨时间、研磨方式决定着颜料在油墨体系中的分散性。换言之,研磨分散工艺条件直接影响到UV喷墨油墨的性能。
1 实验部分
1.1 实验原材料
氧化锆珠:直径分别为2.0~2.2mm,1.6~1.8mm,1.0~1.2mm。预聚物:聚酯丙烯酸酯(Viajet100,氰特公司)。单体:丙烯酸2-乙氧基乙酯(EOEOEA,天津天骄公司),1,6己二醇二丙烯酸酯(HDDA,天津天骄公司),三羟甲基丙烷三丙烯酸酯(TMPTA,天津天骄公司)。
颜料:碳黑(R250,卡博特公司)。
1.2 仪器设备
研磨设备:GJ-2S型高速研磨机(青岛海通达公司)。
测试仪器:Microtrac的S3500型激光粒度仪(美国microtrac公司)。
1.3 实法
UV喷墨油墨的制备分两步进行:室温条件下,按照既定,将颜料、预聚物、部分单体和分散剂混合搅拌进行预分散15min,倒入GJ-2S型高速研磨机,加入特定型号的氧化锆珠以2000r/min的速度研磨,使颜料在连结料中充分润湿分散,在佳研磨时间取出较优色浆。然后,将色浆与成膜预聚物、单体和引发剂混合制备成油墨。在这两步过程中,色浆的分散性能基本上决定了油墨的分散性能。所以,色浆的分散性很重要。
经研磨后的色浆在激光粒度仪上进行油墨粒径测试,从测试的粒径分布图上可以得到油墨的粒径大小及其分布。
2 实验结果与分析
2.1 研磨时间对UV喷墨油墨分散性的影响
固定UV喷墨油墨色浆的,色浆的颜基比
为3∶1,采用不同大小的研磨珠研磨色浆,研磨珠的总量为75mL,研磨色浆的总量是100g。利用激光粒度仪测试不同研磨时间获得的色浆粒径,以油墨95%的粒径大小进行比较,如图1所示。
从图1可以看出,每种珠在不同的研磨时间下有不同的粒径大小,且随着研磨时间的增加,所得到的油墨粒径一般都是先减小后又逐渐。研磨初始阶段,在研磨珠的作用下,颜料粒子逐渐被分散,颜料粒子之间的间隙逐渐被预聚物填充,当研磨作用到一定程度时,颜料粒子处于均匀分散的状态,表现为UV喷墨油墨体系中颜料粒子的粒径间的增加而逐渐减小。但随着研磨时间的增
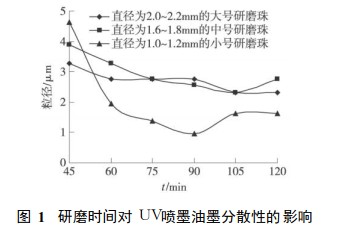
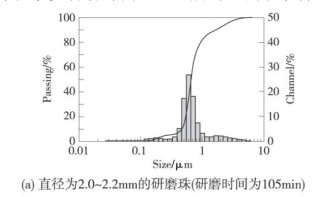
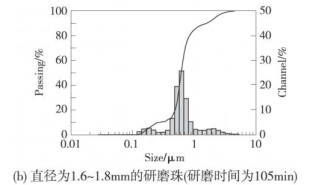
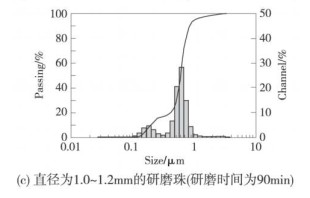
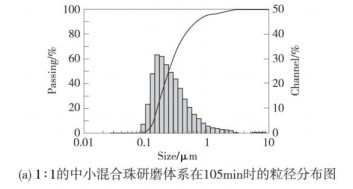
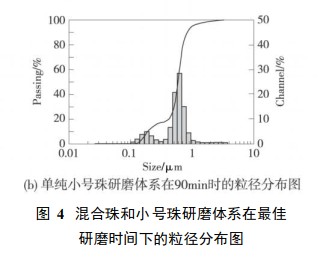
从图1可以看出,每种珠在不同的研磨时间下有不同的粒径大小,且随着研磨时间的增加,所得到的油墨粒径一般都是先减小后又逐渐。研磨初始阶段,在研磨珠的作用下,颜料粒子逐渐被分散,颜料粒子之间的间隙逐渐被预聚物填充,当研磨作用到一定程度时,颜料粒子处于均匀分散的状态,表现为UV喷墨油墨体系中颜料粒子的粒径间的增加而逐渐减小。但随着研磨时间的增
加,经过前期研磨后得到的颜料的粒径较小,其比表面能较大,颜料粒子与颜料粒子之间会发生聚集,使得油墨的粒径又逐渐。所以,在研磨时有一个佳研磨时间的问题,即在这个时间下研磨得到的油墨粒径小。从图1可以看出,直径分别为2.0~2.2mm,1.6~1.8mm,1.0~1.2mm的3种研磨珠对应佳的研磨时间分别为105min,105min,90min。这是由于小号珠比表面积大,即与颜料的作用面积大,效率高,使得油墨粒径在很短的时间内迅速下降,很快达到佳研磨状态。
2.2 研磨珠大小对UV喷墨油墨分散性的影响
从图1可以看出,3种粒径大小不同的珠在不同的研磨时间下得到的油墨的粒径并不相同。利用激光粒度仪测试这3种研磨珠在佳研磨时间所获得的油墨粒径分布,如图2所示。
从图2可以看出,3种粒径大小不同的珠在佳研磨时间下所对应的油墨的粒径分布和粒径大小不同。直径为1.6~1.8mm的中号珠和直径为2.0~2.2mm的大号珠在佳研磨时间105min下所对应的粒径分布要比直径为1.0~1.2mm的小号珠在佳研磨时间90min所对应的粒径分布要
宽。由图2还可看出,3种珠在各自的佳研磨时间下所研磨得到的油墨粒径不同,大号珠在95%的粒径大小对应的粒径为2.312μm,中号珠在95%的粒径大小对应的粒径为2.31μm,而小号珠在95%的粒径大小下对应的粒径为0.972μm,要比2.31μm小得多。这是因为在研磨过程中,直径为1.0~1.2mm的小号珠本身直径较小,所以其作用面积较大,对颜料的作用力大,使得油墨粒径整体迅速下降,后得到的粒径也较小;而直径为1.6~1.8mm的中号珠和2.0~2.2mm的大号珠由于其本身粒子直径较大,比表面积小,作用面积小,所以对颜料的作用力比较小,不能够使得油墨粒径整体下降而只能使部分油墨粒径下降,所以,对应的油墨粒径的分布范围比较宽,得到的油墨粒径比较大[3]。且从图2还可看出,研磨珠的粒径越小,对应得到的小粒径油墨越多,大粒径油墨越少。从图2看,直径为1.0~1.2mm的小号珠的粒径分布相对于大号珠和中号珠而言,整体向小粒径方向偏移,即小粒径的油墨占的比例较大。在选择研磨珠尺寸时,主要考虑两个方面:一是必须便于从基料中分离研磨介质;二是要获得更高的研磨效率[4]。
通过比较可知,在佳研磨时间下,大号珠和中号珠这两种珠的研磨效果大体相同,而小号珠的研磨效果要比它们好得多,所需的研磨时间也短,且较易从基料中被分离,操作较方便。所以,选用直径为1.0~1.2mm的小号珠研磨油墨较理想。
2.3 混合大小研磨珠对油墨分散性的影响
将不同大小的研磨珠混合来研磨油墨,以考察混合大小研磨珠对油墨分散性的影响。由于本实验所选用的大号研磨珠与中号研磨珠的研磨效果相似,因此只将中号研磨珠与小号研磨珠以1∶1的比例混合研磨油墨,测试所获得的油墨的粒径,并与单纯使用中号、小号研磨珠的研磨效果相比较,如图3所示。
从图3可以看出,不同大小珠以一定比例混合
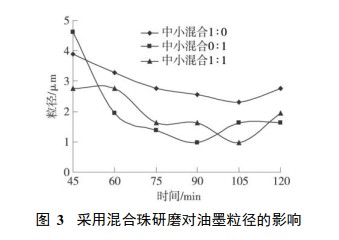
与采用同样大小的珠子研磨所得到的油墨粒径大小不同。这是因为在研磨时,研磨珠大小不同会对颜料分散的作用力不同,而当大小珠混合时,由于珠粒径不同,对较小和较高的颜料附聚体的作用应力也各不相同。由图2分析可知,单纯采用粒径为1.0~1.2mm的小号珠研磨效果好,所以,下面主要对采用1∶1的中小混合珠和单纯小号珠的研磨效果进行比较。从图3可以看出,用1∶1的中小混合珠研磨时,在研磨的初始阶段,油墨粒径下降得比较缓慢,研磨到105min时,油墨的粒径才达到小0.972μm,这是由于混合珠对较小和较高的颜料附聚体的作用应力各不相同,可在短时间内使粒径分布比较均匀且在一定的范围之内,即粒径不会陡然下降而是整体平稳下降,这样能够使大小不同的颜料粒子粒径都得到很好的研磨。但由于前期的研磨使得整体粒径都下降,使得颜料粒子的比表面积较大,后期的继续研磨会使得颜料粒子聚集比较快。从图3还可看出,到120min时,粒径从小的0.972μm变为1.944μm。而采用小号珠单独研磨时,由于珠本身的比表面积较大,对颜料的作用面积大,研磨的过程中油墨的粒径下降得比较快。从图3可看出,在90min时研磨的油墨粒径达到小0.972μm,且在后期颜料粒子的聚集比较缓慢,在105min和120min时,粒径达到1.635μm。
与采用同样大小的珠子研磨所得到的油墨粒径大小不同。这是因为在研磨时,研磨珠大小不同会对颜料分散的作用力不同,而当大小珠混合时,由于珠粒径不同,对较小和较高的颜料附聚体的作用应力也各不相同。由图2分析可知,单纯采用粒径为1.0~1.2mm的小号珠研磨效果好,所以,下面主要对采用1∶1的中小混合珠和单纯小号珠的研磨效果进行比较。从图3可以看出,用1∶1的中小混合珠研磨时,在研磨的初始阶段,油墨粒径下降得比较缓慢,研磨到105min时,油墨的粒径才达到小0.972μm,这是由于混合珠对较小和较高的颜料附聚体的作用应力各不相同,可在短时间内使粒径分布比较均匀且在一定的范围之内,即粒径不会陡然下降而是整体平稳下降,这样能够使大小不同的颜料粒子粒径都得到很好的研磨。但由于前期的研磨使得整体粒径都下降,使得颜料粒子的比表面积较大,后期的继续研磨会使得颜料粒子聚集比较快。从图3还可看出,到120min时,粒径从小的0.972μm变为1.944μm。而采用小号珠单独研磨时,由于珠本身的比表面积较大,对颜料的作用面积大,研磨的过程中油墨的粒径下降得比较快。从图3可看出,在90min时研磨的油墨粒径达到小0.972μm,且在后期颜料粒子的聚集比较缓慢,在105min和120min时,粒径达到1.635μm。
综上所述,采用1∶1的中小混合珠研磨体系的研磨效果也能够达到单纯采用小号珠研磨体系的研磨效果,但所需的时间较长。
为了地比较1∶1的中小混合珠研磨体系和单纯小号珠研磨体系的研磨效果,我们对二者在佳研磨时间下的粒径分布图进行比较,如图4所示。
从图4可以看出,在各自的佳研磨时间下,1∶1的中小混合珠研磨体系相对于单纯小号珠的
研磨体系研磨得到的油墨粒径明显地整体偏向于小粒径分布,这是因为它是由小珠和中珠混合而成的,是混合体系,对较小和较高的颜料附聚体的作用力不同,研磨时能够使得油墨粒径整体得到下降,所以,后得到的更小粒径的油墨相对较多。
因此,由图4可知,采用1∶1的中小混合珠研磨体系的研磨效果比采用单纯小号珠的研磨体系要好,获得的更小粒径的油墨要多一些,研磨得到油墨90%的粒径在0.656μm以下,而使用小号珠研磨得到油墨90%的粒径在0.815μm以下。
3 结 论
1)在UV喷墨油墨的研磨过程中,研磨时间对油墨的粒径有很大影响。随着研磨时间的增加,油墨的粒径呈现先减小后增加的趋势,且不同大小的研磨珠对应的佳研磨时间也不同。本实验条件下,直径为2.0~2.2mm、1.6~1.8mm、1.0~1.2mm的大、中、小号3种研磨珠对应的佳研磨时间分别为105min、105min和90min。
2)在UV喷墨油墨的研磨过程中,研磨珠的大小对油墨的粒径有很大影响[5]。研磨珠越小,得到的油墨粒径分布越窄,且研磨效果越好,研磨效率越高,但过小的研磨珠会造成操作不便。本实验使用直径为1.0~1.2mm小号珠的研磨效果较好,研磨得到油墨95%的粒径在0.972μm以下。
3)将不同大小的珠混合起来进行研磨,能提高研磨效果。本实验条件下,采用1∶1的中小混合珠研磨体系的研磨效果比采用单纯小号珠的研磨体系要好,获得的更小粒径的油墨要多一些,但达到佳研磨效果所需的时间稍长,研磨得到油墨90%的粒径在0.656μm以下。