新闻中心
二氧化钛分散技术研究
作者:admin日期:2020-07-25阅读
研究了TiO2颗粒“打浆分散—砂磨”组合工艺分散技术。采用黏度和粒度表征TiO2颗粒的分散状况,通过透射电镜观察分散前后TiO2颗粒大小和形貌的变化情况。探讨了分散剂种类、分散剂加量、砂磨介质粒径和砂磨时间对TiO2颗粒分散效果的影响。结果表明,TiO2颗粒的佳分散工艺为:硅酸钠作为分散剂,添加量为TiO2质量分数的0.2%,采用粒径为0.4μm的氧化锆珠砂磨25min,平均粒径为265nm,粒度大小均匀,分散效果稳定。
引言
经回转窑煅烧、破碎后的二氧化钛粉体粒径在320~350nm,分布较宽,由于表面界面效应、体积效应和量子尺寸效应等作用,又使粉体出现大量的软团聚和硬团聚。这将导致在后序的无机包膜过程中,二氧化钛不能呈单分散状态,包膜效果不佳,终会影响产量,如产品的颜料性能和耐候性降[1]。因此,二氧化钛的分散是金红石型二氧化钛生产的重要环节。
报道粉体分散机理研究的文献较多。针对不同的分散方法进行分散机理研究,分散方法分为物理分散和化学分散两种。其中,物理方法主要是通过设计合适的机械分散使得分散有效体积和利用率得以提高,物理分散方法械搅拌、超声分散及研磨等[2]。而化学分散则是通过加入可电离的分散剂起作用,分散剂在水中溶解电离出大量的阴离子和阳离子,在颗粒表面形成带相反电荷的双电层,产生静电斥力,阻止颗粒的团聚。颗粒的分散按不同的分散体系划分,有固体颗粒在液相中的分散,固体颗粒在气相中的分散,液体颗粒在另一种液体中的分散三种。二氧化钛的分散属于颗粒在液体中的分散,分散过程包括以下三个阶段:
①颗粒被液体润湿;
②在机械力的作用下,将团聚体打开成原生粒子或较小的团聚体;
③采用物理或化学方式,将打开的原生粒子或较小团聚体分散稳定,阻止再团聚的发生[2-4]。由于二氧化钛生产工艺的特殊性,采用单一的分散手段,不能达到理想的效果。笔者尝试将物理分散和化学分散结合,研究了分散剂的种类、分散剂的加量、研磨介质的选择及研磨时间对二氧化钛分散稳定性的影响,形成了打浆分散-砂磨组合工艺,并确定较佳的工艺参数,提高钛白粉的产量。
①颗粒被液体润湿;
②在机械力的作用下,将团聚体打开成原生粒子或较小的团聚体;
③采用物理或化学方式,将打开的原生粒子或较小团聚体分散稳定,阻止再团聚的发生[2-4]。由于二氧化钛生产工艺的特殊性,采用单一的分散手段,不能达到理想的效果。笔者尝试将物理分散和化学分散结合,研究了分散剂的种类、分散剂的加量、研磨介质的选择及研磨时间对二氧化钛分散稳定性的影响,形成了打浆分散-砂磨组合工艺,并确定较佳的工艺参数,提高钛白粉的产量。
1试验
1.1试验原料及仪器
试验原料:金红石二氧化钛初品(攀钢集团钛业有限公司),单异丙醇胺(巴斯夫有限公司),硅酸钠(成都市科龙化工试剂厂),六偏磷酸钠(天津市科密欧化学试剂有限公司),聚羧酸分散剂(市售),聚丙烯酸分散剂(市售),氢氧化钠(成都市科龙化工试剂厂),均为工业纯。不同粒径的氧化锆珠(国内某锆珠厂)。
试验仪器:Zetasizernano-ZS90激光粒度仪(英国马尔文公司),Brookfield旋转黏度仪(美国Brookfield公司),pHs-3型pH计(上海雷磁仪器厂),JEM-21000F场发射透射电子显微镜INCA能谱仪(日本电子株式会社),SF型分散砂磨机(江阴精细化工机械有限公司)。
试验仪器:Zetasizernano-ZS90激光粒度仪(英国马尔文公司),Brookfield旋转黏度仪(美国Brookfield公司),pHs-3型pH计(上海雷磁仪器厂),JEM-21000F场发射透射电子显微镜INCA能谱仪(日本电子株式会社),SF型分散砂磨机(江阴精细化工机械有限公司)。
1.2试验过程
1.2.1二氧化钛分散砂磨
量取500mL蒸馏水于烧杯中,将分散剂按照一定质量分数加入,不断搅拌,加入300g二氧化钛粉末,并不断搅拌,并加入氢氧化钠溶液,调节pH值至9.5~10.0,加入300g氧化锆珠,在分散砂磨机中进行一定时间的砂磨分散,过滤得到分散后的二氧化钛浆料。
1.2.2分析测试
粒度测试:量取0.5mL分散后的二氧化钛浆料,加入50mL六偏磷酸钠水溶液中(六偏磷酸钠质量分数为0.05%),超声分散10min;量取上述分散好的溶液5mL加入50mL六偏磷酸钠水溶液,再超声分散5min;取上述终分散好的水溶液进行粒度检测。
黏度测试:直接测量二氧化钛浆料对剪切应力(通过特定型式转子的旋转产生)的应变值,单位为Pa·s。量取500mL分散后的二氧化钛浆料与烧杯中,选择62号转子,转速为30r/min,读取黏度值,每个样品检测三次,取平均值。
2结果与讨论
2.1分散剂种类对分散效果的影响
将分散剂加入到固液分散体系中,使其在颗粒表面吸附,改变颗粒的表面性质,从而改变颗粒与液体介质、颗粒与颗粒之间的相互作用,致使体系呈稳定的分散状态。常用的分散剂种类有无机电解质、表面活性剂及高分子,笔者选择硅酸钠、六偏磷酸钠,单异丙醇胺及聚羧酸盐、聚丙烯酸钠五种分散剂进行试验。试验条件为:100mL蒸馏水,分散剂加量为0.02g,搅拌均匀后,加入10gTiO2,搅拌30min,检测TiO2浆料的Zeta电位,结果如表1所示。
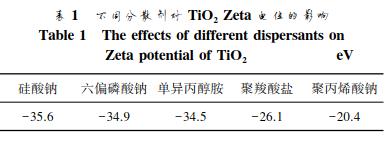
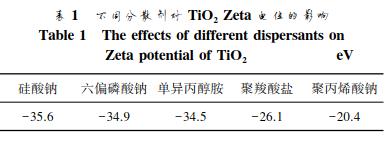
从表1可知,采用硅酸钠、六偏磷酸钠和单异丙醇胺作分散剂时,TiO2浆料的Zeta电位值较大。硅酸钠、六偏磷酸钠和单异丙醇胺等无机电解质的加入,一方面,增加了TiO2颗粒表面的双电层,提高TiO2颗粒表面的Zeta电位值;另一方面,无机电解质TiO2颗粒表面对水的润湿程度,颗粒之间的团聚。聚羧酸盐和聚丙烯酸钠属于高分子聚合物类分散剂,其分子结构中的羧基可与TiO2颗粒表面的羟基发生较强的氢键作用,能让高分子吸附于TiO2颗粒表面,从而形成一层高分子保护膜,可诱发很强的空间排斥效应[2]。加上带有相同电荷的粒子靠近时产生静电斥力,有效地阻止颗粒间的团聚。因此,高分子分散剂能降TiO2浆料的黏度,但是Zeta电位值较[3、5-7]。
2.2分散剂加量对分散效果的影响
采用硅酸钠、六偏磷酸钠、单异丙醇胺做分散剂,研究不同分散剂对TiO2分散效果的影响。试验条件为:500mL蒸馏水,按一定比例加入分散剂,搅拌均匀后,加入300gTiO2,搅拌30min,检测TiO2浆料的黏度,试验结果如图1所示。
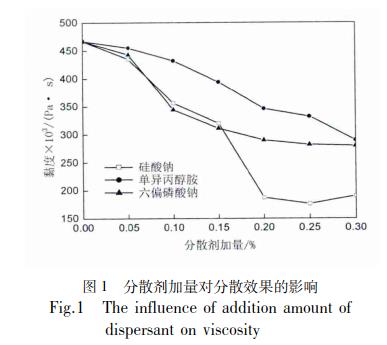
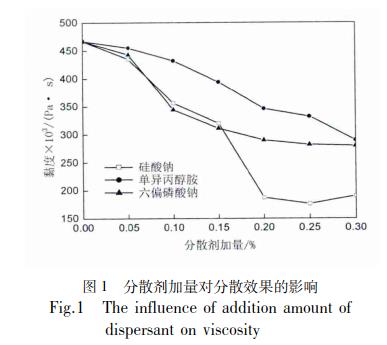
从图1可知,随着分散剂用量的增加,TiO2浆料的黏度呈下降趋势。但是分散剂的加量增加到0.25%以后,TiO2浆料的黏度又有所升高。这是因为,分散剂加入量的增加,经电离后吸附在TiO2颗粒表面的阴离子增多,Zeta电位升高,颗粒表面的双电层产生的斥力,颗粒分散性,浆料的黏度降。随着分散剂的过剩,过多的分散剂游离在溶液中,会导致阴离子浓度加大,压缩双电层,降颗粒之间的静电斥力,同时,过多的电解质会发生桥联作用,使得颗粒团聚加剧,浆料体系黏度增加[7-9]。因此,分散剂的佳添加量为0.2%。
2.3砂磨介质对分散效果的影响
分散剂加入TiO2浆料中,打浆分散,只能将颗粒之间由于静电作用力和范德华力作用聚集的软团聚体打开,而不能将颗粒之间由于液相桥或固相桥结合形成的硬团聚体打开。此时,需要借助机械研磨的手段,将硬团聚体打开,并将较大的颗粒研磨细,修整颗粒的不规状。笔者采用湿法砂磨的工艺,砂磨操作应该控制的工艺参数很多,如,砂磨介质的选择,介质大小的选择,砂磨时间等[3]。TiO2颗粒较硬,一般选择氧化锆珠作为砂磨介质,此处只对砂磨介质球径和研磨时间进行研究。采用硅酸钠作为分散剂,研究不同砂磨介质粒径(0.2、0.4、0.8μm)对TiO2分散效果的影响。试验条件为:500mL蒸馏水,加入分散剂,加量均为0.2%(质量分数),搅拌均匀后,加入300gTiO2,搅拌30min,加入300g氧化锆珠,取砂磨过程中的TiO2浆料,检测其粒度。试验结果如图2所示。
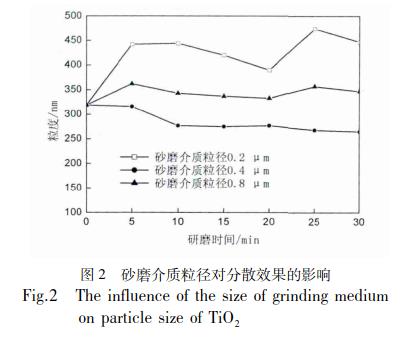
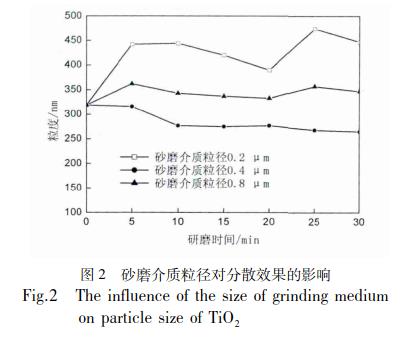
从图2可知,砂磨介质粒径对产品粒度的影响较大。砂磨介质粒径为0.4μm时,产品粒度小,砂磨30min后,平均粒径下降至265nm;当砂磨介质粒径大于或小于这个粒径时,砂磨效果均不理想,产品粒度大于300nm。分析其原因,当砂磨介质粒径大时,砂磨介质与桶壁、砂磨介质与介质之间的作用力强,而砂磨介质与物料之间的作用力相对较弱,达不到佳的砂磨效果;而当砂磨介质粒径小时,受到溶液浮力作用相对较大,抵消部分,降了砂磨效率。因此,不同粒度的物料研磨,需选择不同粒径的砂磨介质,TiO2颗粒研磨,佳的砂磨介质粒径为0.4μm。
2.4砂磨时间对分散效果的影响
采用硅酸钠、六偏磷酸钠、单异丙醇胺作分散剂,研究不同砂磨时间对TiO2分散效果的影响。试验条件为:500mL蒸馏水,加入分散剂,加量均为0.2%(质量分数),搅拌均匀后,加入300gTiO2,搅拌30min,加入300g氧化锆珠(粒径0.4μm),取砂磨过程中的TiO2浆料,检测其粒度,试验结果如图3所示。
从图3可知,采用单异丙醇胺和六偏磷酸钠作分散剂时,研磨初期,随着砂磨时间延长,TiO2颗粒的平均粒径逐渐减小,但是,随着砂磨时间进一步延长,TiO2颗粒的平均粒径反而,出现了“逆研磨”现象,主要原因是,研磨初期,TiO2颗粒之间、TiO2颗粒与砂磨介质之间的机械碰撞、互相研磨促使TiO2颗粒的粒度变小,比表面积;随着砂磨的进一步进行,颗粒继续细化,比表面积进一步增加,而又得不到充分的分散,那么,TiO2颗粒为了克服较大的表面能,在静电作用力、范德华力、机械力的作用下,又将团聚在一起,从而减小比表面积,降表面张力[5、8-10]。硅酸钠作为分散剂时,则未出现“逆研磨”现象,这是因为,硅酸钠能使TiO2颗粒得到充分的分散,不会发生再次团聚。硅酸钠的研磨佳时间为25min,限粒度为265nm。
2.5TiO2颗粒形貌分析
为了直观地观察分析“分散—研磨”前后TiO2颗粒的形貌变化情况,对“分散—研磨”前后TiO2颗粒进行透射电镜分析,结果如图4所示。
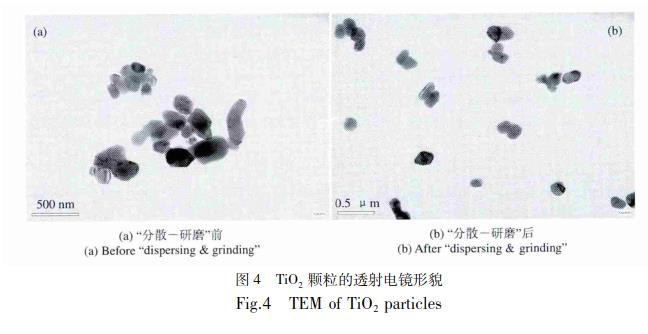
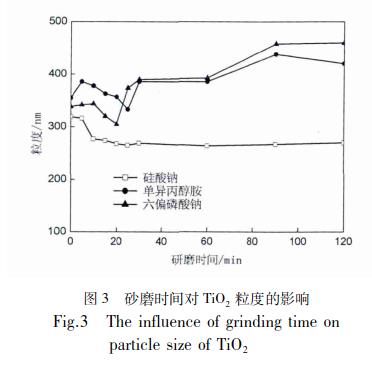
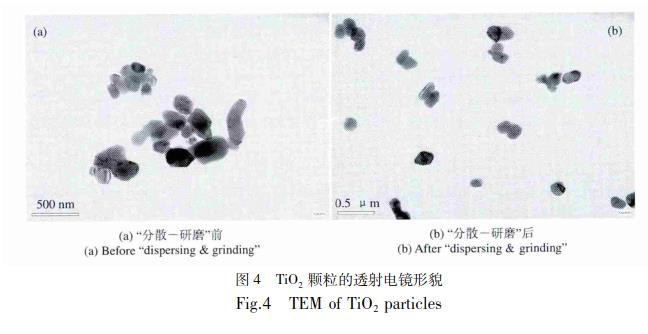
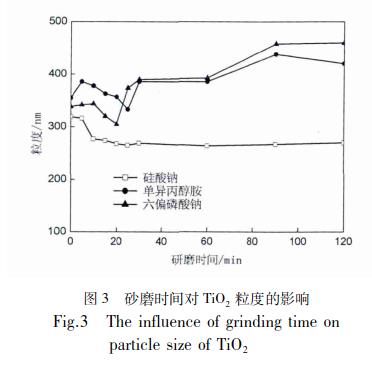
从图4可以看出,分散前,TiO2颗粒处于团聚状态,经过“分散—研磨”后,TiO2颗粒得到呈现充分分散的状态;TiO2颗粒尺寸由300nm细化到260nm左右;颗粒的大小更加均匀,粒径分布变窄;不规状得以修正,形貌更趋向于球形;颗粒呈单分散状态。通过上述方法分散后的TiO2浆料,颗粒粒径小、大小均匀,颗粒呈单分散状态,黏度,有利于包膜剂均匀沉积到TiO2颗粒表面,提高包膜效果,从而提高产品的颜料性能和应用性能。
3结论
1)通过对比不同种类分散剂对TiO2浆料分散性的影响,采用硅酸钠和六偏磷酸钠作分散剂,浆料的Zeta电位值较大,浆料的黏度较,分散效果理想。
2)研磨介质的粒径对研磨效果影响较大,砂磨介质粒径为0.4μm时,产品粒度小,砂磨30min后,平均粒径下降至265nm。
3)分散剂在研磨过程中起着非常重要的作用,采用六偏磷酸钠和单异丙醇胺做分散剂时,会发生“逆研磨”现象;但是,采用硅酸钠做分散剂时,TiO2颗粒能够得到充分的分散,次发生团聚,不会出现“逆研磨”现象。
4)该研究结果对与钛白粉颗粒分散类似的同类粉体颗粒如SiO2、高岭土、CaCO3等的分散技术具有参考价值。