行业知识
国产氧化锆粉体的表面改性处理
作者:admin日期:2020-05-13阅读
采用卧式砂磨机对国产氧化锆粉体进行表面改性处理。结果表明,虽然磨细处理可以有效提高粉体烧结活性,但必须有适当的造粒工艺相配合才能获得有应用价值的粉体。国产氧化锆粉体改性处理后,烧结试样抗弯强度降的主要原因是存在大尺寸缺陷。分析了高温煅烧处理对国产氧化锆粉体性能的影响,初步认为提高粉体相变的稳定性有利于获得高性能氧化锆粉体。
四方多晶氧化锆陶瓷(TZP)由于具有优异的室温力学性能,近年来,在工业、通讯、日用品等领域得到越来越广泛的应用。众所周知,使用高性能陶瓷粉体是获得高性能陶瓷制品的必要条件,国内学者围绕高性能氧化锆粉体已开展了大量的研究工作[1,2],多个的氧化锆粉体也已实现了商品化,但国产粉体性能与国外同类产品相比仍有明显的差距,如日本Tosoh 造粒粉在1400℃即可烧结致密,且抗弯强度可达1000MPa 以上,而国产造粒粉一方面需要较高的烧结温度,另外烧结后抗弯强度较。干压成型作为陶瓷的重要成型工艺应用广泛,而粉体造粒处理是干压成型的关键,随着国内市场对氧化锆陶瓷的大量需求,迫切需要具有优良成型和烧结性能且质量稳定、价格适中的氧化锆陶瓷粉体供应。本实验以国产商品氧化锆粉体为原料,通过进一步细化和表面改性处理,探讨提高国产粉体烧结性能和成型性能的途经。
实 验
采用德国耐驰卧式搅拌磨(型号:LME1)对国产3Y-TZP 氧化锆粉体进行研磨,搅拌速度为2000r/min,研磨介质采用Φ0.5 mm的氧化锆微珠,加入1.5%聚丙烯酸铵为分散剂,0.8%的PVA 为粘结剂。将研磨的粉料配制成体积分数为10%的陶瓷浆料,进行手工造粒表面改性和喷雾造粒处理。造粒粉体经干压成型和200 MPa 冷等静压处理后,分别在1350、1400、1450 和1500 ℃保温1.5 h 进行无压烧结。样品经磨削加工制成标准试条,采用三点弯曲进行强度测试。采用阿基米德法测试密度。采用SEM 观察断口和粉体形貌。采用激光粒度分析仪进行粒度分析。
2 结果与分析
2.1 粉体的磨细处理
图1 是实测的研磨时间与粉体粒度的关系曲线。
由图1 可知,经过2 h 磨细后粉体的平均粒度D50 已经从原始粉体的0.623 μm 减小到约0.2 μm,但此时D90 数值仍然偏高,说明粉体粒度分散较宽。随着研磨时间的增加,粉体的粒度分布逐渐变窄。考虑到成本因素,后确定研磨时间为8 h。图2 是研磨8 h 后的粉体粒度分布分析结果。可见其平均粒度D50 已降到0.115 μm,与原始粉体相比不粒度大大细化,而且分布更窄,达到了国外先进粉体的指标要求。
2.2 粉体的喷雾造粒处理
流动性和堆积密度是衡量粉体成型性能的重要指标。本实验磨细处理的粉体配制成浆料进行喷雾造粒试验。控制入口温度为350 ℃,出口温度约120 ℃,
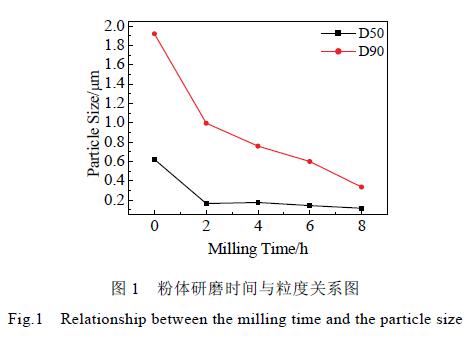
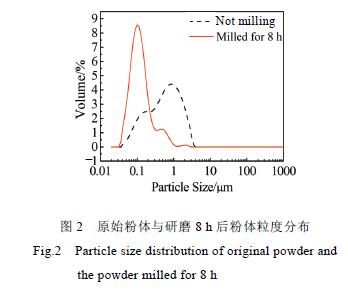
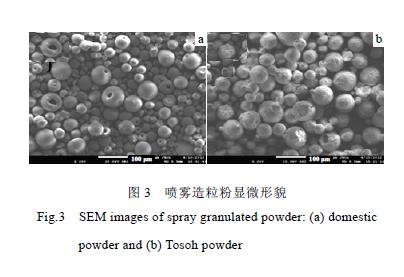
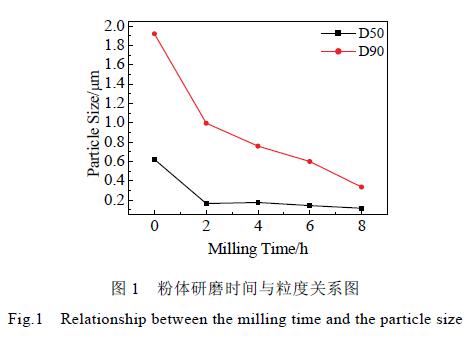
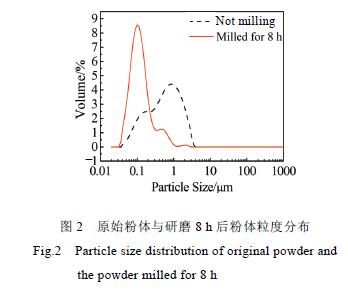
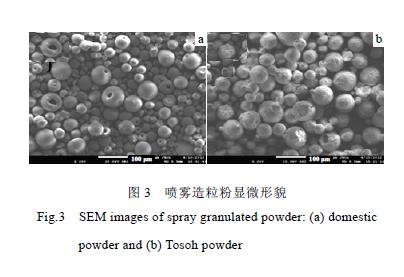
进料速度控制在1~2 L/h。图3 是喷雾造粒后的粉体和日本Tosoh 造粒粉的扫描电镜照片。由图可知,国产粉经过喷雾造粒变成了规则的球形颗粒,与日本造粒粉相比有较多的苹果状空心颗粒,且表面较致密光滑。喷雾造粒粉体的松装密度为1.42 g/cm3,高于日本造粒粉体的1.30 g/cm3。造粒颗粒表面光滑有利于提高粉体的流动性,但颗粒太致密、强度过高会造成在成型过程中不易被压碎,而且过多的空心颗粒会导致生坯缺陷增加。
2.3 粉体的烧结性能
试样烧结致密度与烧结温度的关系曲线如图4 所示。与原始粉体相比,磨细后经过手工造粒粉体在1350~1400 ℃已基本烧结致密,温烧结性能明显体提高,但磨细后喷雾造粒的粉体,其烧结性能却显著下降。图5 是试样抗弯强度与烧结温度的关系曲线。可见经磨细改性处理后抗弯强度明显降。值得关注的是,在1350~1400 ℃烧结条件下尽管磨细后手工造粒粉体的烧结密度高于原始粉体,但其抗弯强度明显于后者。图6 是1400 ℃烧结氧化锆陶瓷的扫描电镜断口形貌。对比图6a,6b,6c 可以看出,虽然原始粉体样品密度不是高,但组织均匀,含有小尺寸分散气孔(图6a);手工造粒样品相对密度较高,
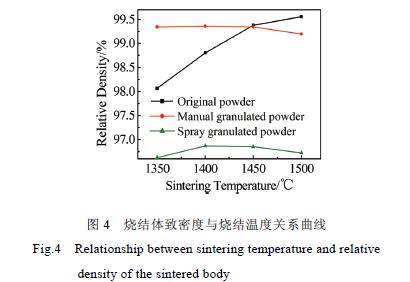
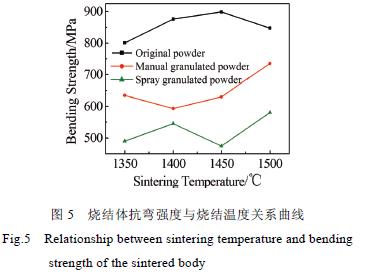
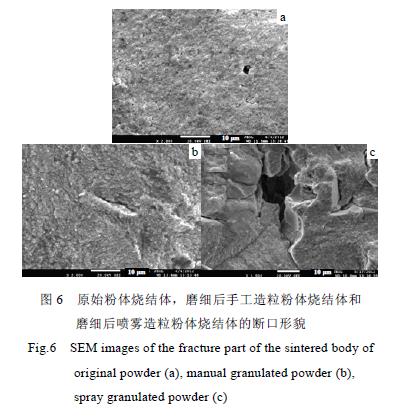
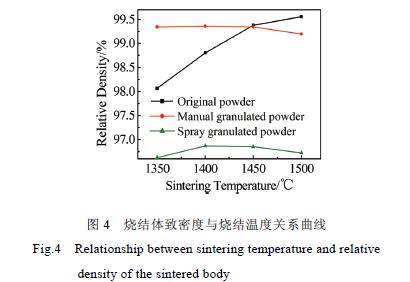
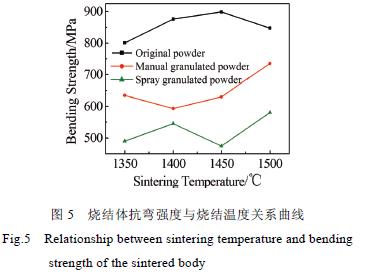
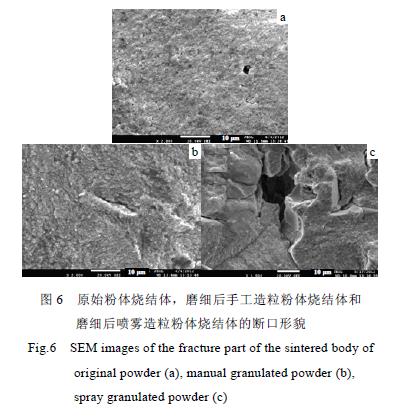
织中含有尺寸较大的缺陷(图6b);喷雾造粒样品密度,其中可以清楚地看到造粒粉体在成型过程中100 μm 100 μma ba10 μmb c10 μm 10 μm–Not milling没有被压碎,烧结后依然保留的痕迹(图6c)。虽然颗粒内部已经烧结致密,但颗粒之间有较大的缺陷。
当试样中存在大尺寸裂纹时,抗弯强度会明显下降,即材料的强度由其中的大尺寸缺陷决定。以上实验结果和分析表明,通过对粉体进行磨细处理虽可显著改善粉体的烧结活性,但必须有其他工艺相配合才能获得具有应用价值的高性能粉体。为了进一步分析改性处理后材料强度降的原因,对不同烧结体进行了XRD 分析,如图7 所示。由此可以看出,国产粉经改性处理后,烧结体中有明显的单斜相存在(图7 中(2)),而相对应的日本粉样品中(图7 中(1))几乎看不到单斜相。这说明国产粉体在处理过程中造成了粉体中的氧化钇分布的不均匀,导致部分四方相氧化锆没有被有效地稳定到室温。这可能是除造粒因素之外影响烧结体抗弯强度的另一个原因。
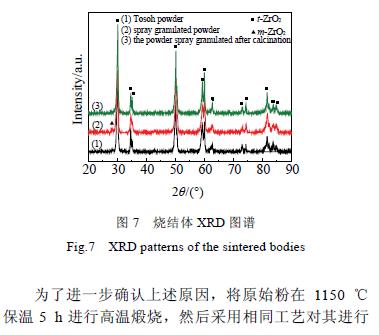
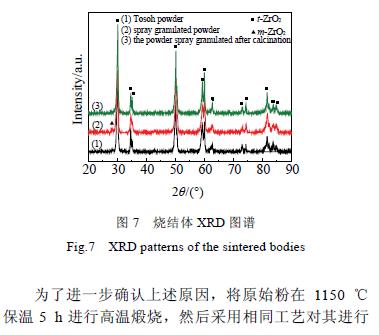
改性处理。结果发现,卧式砂磨机磨6 h,粉体的粒度D50 达到0.5 μm,远高于未煅烧处理粉体(见图1),但该粉体经1500 ℃下烧结,其抗弯强度却达到了850 MPa,若将粉体磨细到0.2 μm 以下,其性能会进一步提高。图7 中(3)的XRD 谱线也几乎看不出单斜相,说明高温煅烧后四方相氧化锆的稳定性得到了有效的提高。由此可以认为,原始粉体由于四方相稳定性差,在磨细过程中因表面积增加和一定的温度效应造成粉体表面钇离子溶出,在浆料干燥过程中因某种原因造成粉体中钇元素的局部分布不均匀,从而影响烧结体的终组织和性能,当然该分析还需要进一步的试验验证。
3 结 论
1) 国产氧化锆粉体经过卧式搅拌磨磨细和手工造粒处理后,烧结活性有显著提高,在1400℃烧结条件下,烧结密度可接近99.5%。
2) 国产氧化锆粉体经磨细处理后,烧结试样抗弯强度均于原始粉体的主要原因是存在大尺寸缺陷,因此粉体磨细处理必须有适当的造粒工艺相配合,才能提高粉体成型性能。
3)初步认为提高粉体相变的稳定性有利于获得高性能氧化锆粉体。