行业知识
ITO靶材成形工艺研究进展
作者:admin日期:2020-05-05阅读
ITO靶材主要用于制作液晶显示器、导电玻璃以及太阳能电池等。ITO靶材成形的工艺有冷静压成形、冲压成形、模压成形、挤压成形、凝胶注模成形、注浆成形等等。未来ITO靶材也会快速发展,运用到更多地方。
前 言
ITO是氧化铟锡的英文缩写,电阻率以及透光率高是它的特点,所以ITO靶材非常适合制作太阳能电池、显示器以及导电玻璃。在液晶显示器领域,越来越大的屏幕,色彩的要求越来越高,ITO的发展举足轻重。成形工艺决定着ITO靶材的质量。ITO靶材成形技术基本上可分为两种:干法和湿法。干法的优点是生产方便,不需要进行干燥处理,通过压力成形。湿法成形是需要各种形态的物体混合进行反应,之后进行干燥处理,制作出来的靶材尺寸都比较大。
1 干法成形工艺
1.1 冷等静压成形
冷等静压成形工艺需要在常温环境下进行,将ITO粉按照比例放在高压容器里面,因为液体不会被压缩,所以对液体施加的压力会均匀地分布在各个方向,成形出来的胚体密度会比较均匀。它的缺点是如果对于一些形状不规则以及尺寸较大的靶材会造成受力不均匀的情况,所以可能会出现靶材破裂造成工人中毒的情况。以上问题有相应的解决办法。
在ITO粉冷等静压成形后,卸压的时候利用N级卸压保护,以此来保证靶材密度的均匀性,并且产生ITO薄膜。另一种解决办法则是在ITO粉中加入水、丙酮、无水乙醇,之后放入球磨罐中进行球磨过筛操作,在刚磨具中预先干压,后再执行冷等静压成形工艺。这样操作可以大大降中毒的风险。对于大尺寸的靶材的成形可以通过将ITO浆料放入高频率震动的磨具里,使胚体干燥,后同样执行冷等静压成形工艺就完成了。
1.2 冲压成形
冲压成形顾名思义就是将胚料放入磨具中,然后对磨具施加压力,让它产生形变,出现一定的外形和大小。这种工艺的优点是可以制作出各种形状的工件,尺寸大小也非常精准,利用自动化技术就可批量生产。但是这种方法却运用的较少,因为是产时靶材容易开裂。日本的一位在ITO中加入聚乙烯醇,过筛后加入冲压用的模具中,成型后进行烧结可以得到密度99.2%的靶材,这种靶材即使在与铜背板进行粘合时也不容易出现裂纹。
1.3 模压成形
模压成形是将粉状、颗粒状、纤维状等塑料加入到一定温度下的模具中,然后对其施压,让磨具内的塑料固化成一定形状的工艺。模压成形的优势在于原料的利用率高,性能稳定,尺寸也好掌握,生产效率高。而模压成形的劣势就是ITO靶材的密度且分布的不均匀,从而导致在后续的溅射镀膜时会出现结瘤,会减少产品的使用时长。所以模压成形的ITO原料中要加入聚乙烯醇,增加靶材的密度减小电阻率。在ITO原料中加入聚乙烯醇缩丁醛会靶材的强度,开裂。利用超声波火花刚模压制可以进一步胚体的密度。为了进一步提高组织的均匀性,将含Sn2+盐溶液与纳米In2O3粉体制成ln2O3悬浮液进行混合加入沉淀剂进行沉淀处理,静置陈化后得到In2O3表面均匀,覆盖着SnO2的包覆粉,将所制的ITO粉在130~170MPa压力下压制成形烧结后所制得的靶材组织均匀,密度可达到99%。
1.4 模压成形+冷等静压工艺
将ITO粉末加入聚乙烯醇进行造粒,得到球形的ITO 颗粒,然后倒入模具中,在液压机上用5-10MPa压力进行压制,得到粗坯。粗坯再进行包装后,放入冷等静压机中,在大于150MPa压力下,粗坯在液体中各个点受到的压力都是一样的,通过一系列的保压和卸压操作,得到更均匀、致密度更高的素坯。该法得到的素坯放入常压气氛烧结炉中进行高温烧结,得到密度大于99.5%的ITO靶材。该法得到更均匀、密度更高的ITO靶材在溅射镀膜时可有效减少结瘤现象。
2 湿法成形工艺
2.1 挤压成形
将粉料、润滑剂以及粘合剂与水混合,之后将塑料放入磨具内,施加压力使物料成形的工艺就是挤压成形。挤压成形常用来制作炉管、护套管等防火材料,也用于一些电子材料的生产,近期也有用于ITO靶材的生产中。将不同粒度的ITO原料按比例加入去离子水、聚乙二醇以及粘结剂聚乙烯醇球磨过筛,在外界压力的作用下挤出片坯,碾压,在有一定的温度条件下脱脂,再进行烧结可以得到高密度的ITO靶材。这种靶材的强度小,坯料容易出现裂纹表面会有凹坑,所以在ITO靶材的制作中,这种工艺不是很常用。
2.2 凝胶注模成形
2.2 凝胶注模成形
凝胶注模成形的基础是配置浆料,对于浆料的要求是粘度、高固相。然后使浆料中的单体结合,使得浆料固结,这样就会制出密度高、均匀性高的坯体。凝胶注模成形操作便捷、成本,添加物都是物所以在烧结后不会出现杂质。这种技术的出现是得益于陶瓷成形和高分子化学的结合而成。这种工艺多用于组分陶瓷、多孔陶瓷以及梯度陶瓷的制作。利用这种技术制作出来的靶材稳定性高,均匀性好,另可以制作出形状复杂和尺寸较大的靶材。将ITO原料与单体、分散剂、引发剂、胶联剂以及水混合球磨,制作出悬浮液,在将悬浮液放入到磨具内,会产生凝胶反应,终ITO粉体被原位包裹,固化形成柔性的三维网状结构,得到坯体,干燥后进行烧结就会得到密度高的靶材。由于高固含量的浆料的坯体密度大强度大,不易出现开裂的情况,也不会出现形变,所以高固含量可以制出高密度的ITO靶材。为了解决尺寸的问题,在上面的基础上添加缓释剂和增塑剂就可以制作大尺寸的靶材坯体。
在ITO原料中加入的水溶性环氧树脂作为成形剂球磨后凝固,在进行烧结也可以得到密度较高,电阻率相对较的靶材。这样可以大大减小凝胶注模成形时有毒气体对空气的侵蚀,也对工作人员的加以保障。
2.3 注浆成形
注浆成形的原理就是利用多孔石膏磨具会吸收水分的特性,将陶瓷粉配成具有流动性的泥浆,放入到多孔磨具内,水分被吸收后形成了一层泥层,脱水干燥后可以得到坯体。
这种工艺在进行时有三个步骤。先将泥浆倒入模具,靠近模壁的水分先被吸收,逐渐形成一层泥层,后形成雏坯,继续蒸发水分,雏坯收缩,干燥后形成生坯后,脱模完成注浆成形。注浆成形的工艺简单,使用的材料也少,利用基础的模具即可完成。生产出来的坯体稳定性和结构都很高。但是需要大量的人力物力,不能使用自动化设备进行生产。但是在我国仍占据重要地位。现在注浆成形要解决的问题就是坯体容易开裂变形的问题。
实验发现,固含量在60%以下,ITO烧结体硬度。超过85%又容易开裂。所以在ITO浆料中加入粘结剂、保湿剂、润滑剂和消泡剂球磨混合,倒入不锈钢模具内,在模具上方减压抽空排出水分,脱模干燥后的生坯进行烧结得到大尺寸的靶材。另外如果密度不够,可以加入高密度促进剂,这种促进剂是以磷化物为基础。石膏模具双向吸收会对生坯的密度造成影响,也会出现分成剥离的现象。而单向吸水可以有效地解决这种问题,后可制得99.5%密度的靶材。ITO本身难以烧结,所以需要加入多种元素混合而成的专门助烧剂,主要由砷、锑、铋、硒、碲或硼的化合物组成助烧剂,在10Mpa的压力下浇筑30分钟再经过干燥脱脂得到生坯,经过烧结这种ITO靶材的密度可达到99.8%。
3ITO靶材成形技术对比
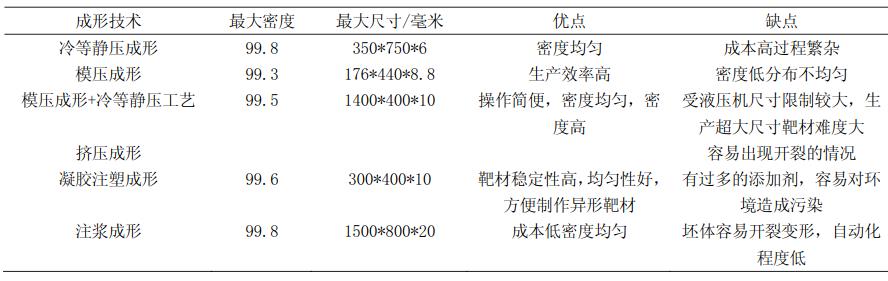
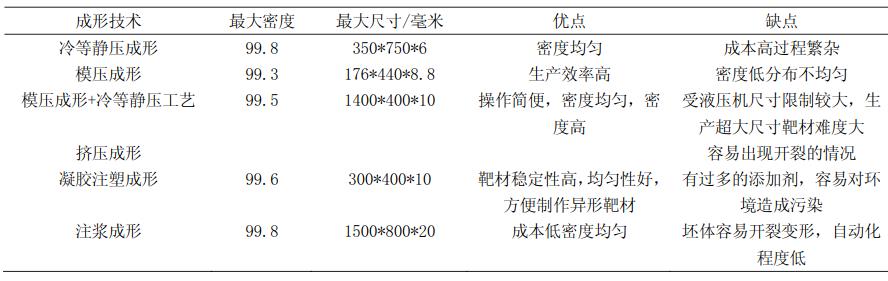
从表中可以看出模压成形+冷等静压工艺和注浆成形在各方面表现都比较均衡,密度高,尺寸大,可满足市场绝大部分需求,且无明显的缺陷,不会污染环境,适合当前市场的需求。
4 展 望
行业的兴起,需要有屏幕显示的支撑,对ITO靶材的需求量越来越多。我国制作ITO靶材的工艺虽多,但是需要找出一个适合的,对制作出来的ITO靶材需要具有高密度,电阻率的特点,另外尺寸可以任意定制。现阶段,我国LCD面板的使用还主要依靠着进口解决,注浆成形技术虽然可以制作出高密度,大尺寸的ITO靶材,但是对于一些产品还有一定的差距,而且在制作时,添加了太多的化学药品,会出现溅射镀膜结瘤的问题。模压成形+冷等静压工艺虽然添加的化学药品较少,但是受到压机和模具尺寸的约束,制作大尺寸ITO靶材难度较大,成本也较高。目前已有国内厂家采取模压成形+冷等静压成型工艺,突破了技术瓶颈,靶材产品通过了方、华星光电、天马等国内面板厂商的测试认证,并逐步批量化供应,开始进行国产化替代。为了早日实现ITO靶材自主国产,需要在成形工艺和烧结阶段做更多的研究,打造出一套完整成形工序。