行业知识
高纯超细石英微粉的制备方法研究
作者:admin日期:2020-08-04阅读
用钇稳定氧化锆珠为研磨介质,对研磨桶内壁和搅拌器都衬以聚氨酯的搅拌磨用于粉磨制备高纯超细石英微粉进行了研究。研究了石英微粉特征参数d 随搅拌粉磨时间延长的变化规律,考察了钇稳定氧化锆珠对石英微粉的污染大小,分析和探讨了1 脚以下超细石英微粉的化学成分和形貌特征。试验证明,用该搅拌磨磨细石英砂可获得1 m以下的高纯超细石英微粉,但难以获得球形石英微粉。
硅微粉有着优良的物理、化学性能。它具有介电性能优异、热膨胀系数、导热系数高、耐温性能好、耐腐蚀、硬度大、纯度高、粒度分布可控、悬浮性能好、白度高、吸油量等诸多优点,是一种用途广的无机粉体材料。硅微粉有结晶硅微粉(即石英微粉)、熔融硅微粉、方石英硅微粉等。根据其不同的质量品级,可将其用于橡胶、塑料、高级油漆、涂料、耐火材料、电器绝缘、电子封装、高档陶瓷、精密铸造等生产领域。其中多种用途对超细石英粉的纯度、粒度和粒度组成有相当严格的要求。将其用作填料,能改善和提高制品的性能,降成本。随着高技术领域的迅猛发展,硅微粉作为填充材料也随之显示出广阔的应用前景。其生产工艺一般包括破碎、粉磨工序。粉磨一般用滚动球磨、搅拌球磨、振动球磨、气流磨等。搅拌磨这种超细粉碎设备,由于其特殊的工作原理,与其它超细粉碎设备相比,具有粉碎效率高、能耗、产品粒度细、污染小、工艺过程简单等优点。由于搅拌粉磨过程产生的作用,还能起到机械产品的效果。但对用钇稳定氧化锆珠为研磨介质、将研磨桶内壁和搅拌器都衬以聚氨酯的搅拌磨用于粉磨制备高纯超细硅微粉,能否获得球形硅微粉、对硅微粉特征参数d 。随搅拌粉磨时间延长的变化规律、钇稳定氧化锆珠对硅微粉的污染程度、对1 Ixm以下超细石英微粉的形貌特征等缺乏研究和报道¨ J。本文针对这些问题展开了研究。
1 试验条件及方法
1.1 主要的原材料和仪器
1.1.1 原材料
(1)石英粉:以脉石英为原料经过选矿提纯后的石英粉,其SiO 的含量为99.94% ,其它成分:微量,小于200口的部分占37.39% ,堆积密度为1.43#cm ;
(2)钇稳定氧化锆珠:莫氏硬度9,直径为3mm,材质密度为6.0 cm ,堆积密度3.8 cm ;
(3)湿磨分散介质:去离子水。
1.1.2 仪器
(1)ZJM20T搅拌球磨机(内壁及搅拌器均衬上聚氨酯),球磨桶容积为6 L,搅拌器可调转速范周:0~1 200 r/min,人料粒度尺寸细于60目,郑州市东方机器制造有限公司生产;
(2)I5一POP型激光粒度分析仪,珠海欧美克科技有限公司生产;
(3)纳米粒度与Zeta电位分析仪:型号为Zetas—izer Nano ZS90,英国Malvern公司生产;
(4)JSM一6380LV型扫捕电子显微镜,日本电子公司生产。
1.2 试法
根据郑州市东方机器制造有限公司的ZJM20T搅拌球磨机的使用说明,计算确定介质球装填量、物料装填量和湿磨分散介质体积。
1.2.1 计算介质球装填量
介质球装填量依下式①计算:


式中:G介一介质球装填量(kg);V桶一搅拌桶容积(L);p介一介质球堆积密度(kg/L);K介一介质球装填系数,一般取0.45~0.5。


1.2.2 确定物料装填量
物料装填量按静态填满介质球间的空隙,并有适当的多余量来计算。物料装填量的计算如下:


式中:G料~ 物料装填量(kg);p,介一介质球的材质密度(kg/L);p料一物料堆积密度(kg/L);K料一物装填充系数,取1.1—1.3,密度易粉磨物料取大值,本文取1.1; 、K介、Pet表示意义同①式。
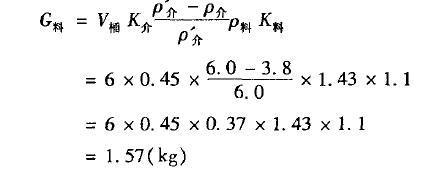
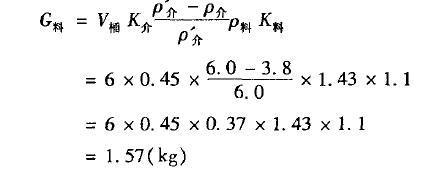
1.2.3 湿磨分散介质体积的确定
采用湿磨时还要加入湿磨分散介质,湿磨分散介质体积应使介质球、粉磨物料在其中有适当的运动空间,具有流动性,以保证粉磨粒度的均匀性。湿磨分散介质的体积可按湿磨分散介质与粉磨物料形成的浆料体积为球磨桶体积的45% ~50%来计算。实际装料时介质球与浆料的总体积为球磨桶体积的75% ~80% 。湿磨分散介质体积按下式计算:


式中: 介一湿磨分散介质体积(L);p,料一粉磨物料材质密度(kg/L); 、G料表示意义同②式。
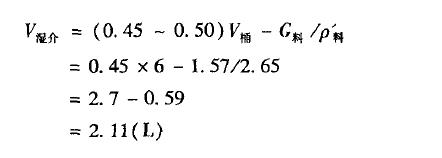
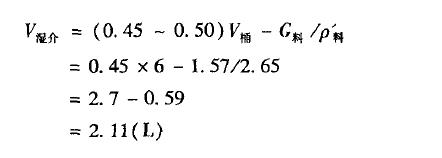
以上对介质球的装填量、粉磨物料装填量和湿磨分散介质体积的计算是原则性的,可根据实际情况进行试验后,择优选定。


通常情况下,料:水:研磨体=1:(0.8—1.1):(1.5~2.3)是适宜范围 J,但亦可根据具体情况调整它们的比例。经计算得:料:水:研磨体=1.57kg:2.11 kg:10.26 kg=1 :1.34 :6.54。由于受材料的尺寸大小和密度的影响,实际选用这个比例是合适的。
1.2.4 选定搅拌球磨机的转速搅拌球磨机的转速定为600 r/min。
1.2.5 测定粉磨不同时间后石英粉的粒度
(1)用欧美克激光粒度分析仪测定粉磨不同时间后的石英微粉的粒度分布;
(2)用纳米粒度与Zeta电位分析仪测定终石英微粉的粒度分布;
(3)用扫描电子显微镜观察分析石英微粉的形貌特征。
2 结果与讨论
2.1 目前对高纯超细硅微粉的一般质量要求纯度要求SiO2含量99.5% ~99.9% ;杂质含量要求:Fe203 0.008% ~0.03% ,A12O3 0.06% ~0.2% ,MgO 0.002% ,Na2O 0.01% ,Ti2O 0.01% ,灼烧失量0.1% ~0.15% ;中位径 ( m):2.5~150。
2.2 粉磨不同时间后石英微粉的粒度变化粉磨不同时间后石英微粉粒度的分布和变化分别见表1和图1所示。
2.2.1 石英微粉特征参数及粒度分布
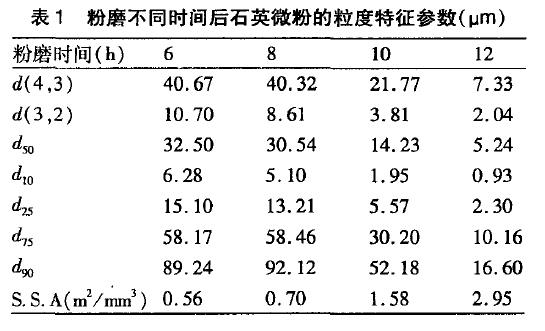
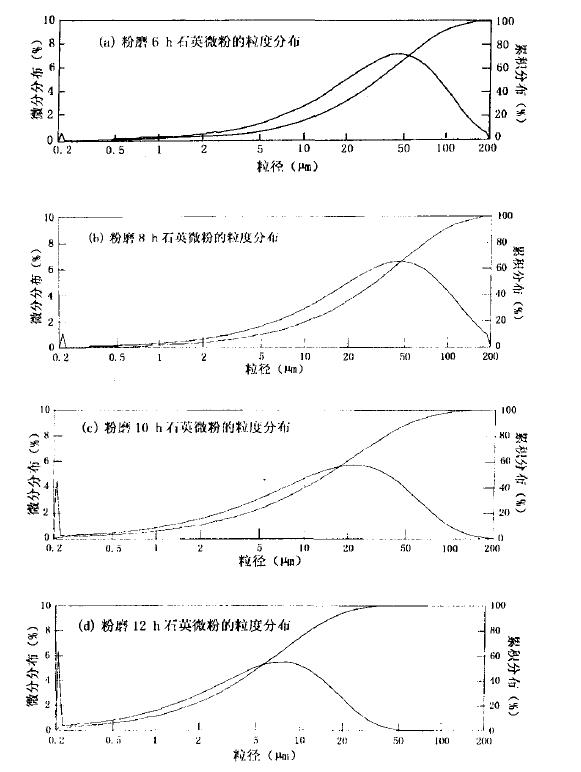
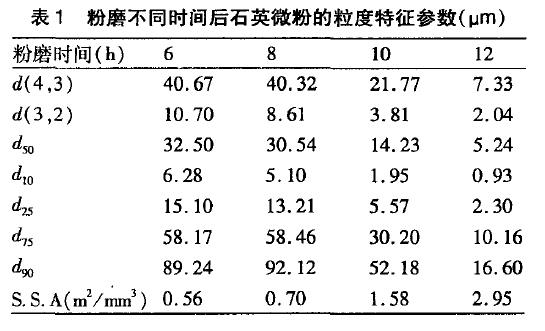
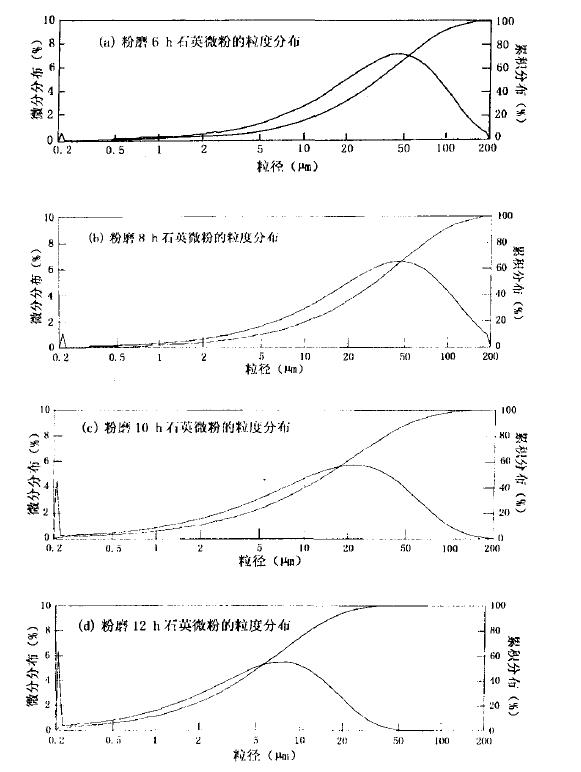
由表1和图1可看出:粉磨6 h后石英微粉的中位径d50是32.50 m,粒径是43.9 m时的微分分布大是7.17% ;大的粒径是169.0 m时,对应的微分分布为1.07%。粉磨8 h后石英微粉的中位径d 。是30.54 m,粒径为43.9 I.zm时微分分布大为6.58% ;大粒径为169.0 m时,对应的微分分布为1.32% 。粉磨10 h后石英微粉的中位径0是l4.23 ,粒径为22.4 时的微分分布大是5.75% ;大的粒径为169.0 m时,其对应的微分分布为0.18% 。粉磨12 h后石英微粉的中位径d5。是5.24 m,粒径为8.14 Ixm时的微分分布大为6.48%;大粒径为72.8 la,m时,其对应的微分分布为0.01% 。可以获得百分含量占99.99% 、粒径为61.5 m以下的石英微粉。
2.2.2 石英微粉粒径特征参数的变化规律
研究粉磨不同时间后石英微粉粒径特征参数的变化规律,可以近似地了解搅拌磨粉磨石英粉的难易程度或粉磨动力学。以粉磨不同时间后的石英微粉粒径特征参数d 。这个50% 累积分布百分数所对应的粒径为参考。由表1得:粉磨6 h、8 h、10 h、12h后的石英微粉粒径特征参数d 。分别为32.50 Ixm、30.54 m、14.23/.zm、5.24/xm。以特征粒径为纵坐标,粉磨时间为横坐标作图,可得粉磨不同时间后粒径特征参数的变化规律曲线,见图2。
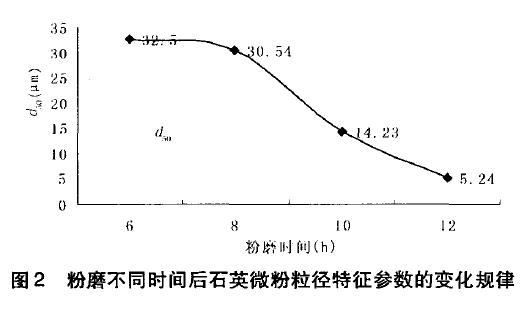
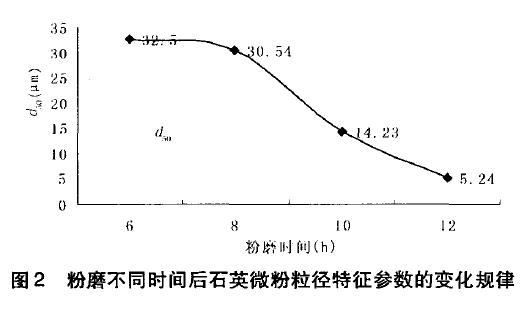
由图2可以看出,当粉磨时间由6 h到8 h,石英粉的特征粒径变化较小,这可能是由于石英砂粒度较粗时,磨介的冲击力相对较小,不足以粉碎石英颗粒。当粉磨时间由8 h延续至12 h,d 。变小的速度明显,说明磨介的粉碎力适合于磨细试验时的石英砂粒度。
2.3 终石英微粉粒度分析
粉磨12 h后,物料粒度在l Ixm左右以下的占11.65% ,故要通过沉降分级才能获取1 Ixm以下的石英微粉。若要增加1 Ixm以下的石英粉体产量,还需继续延长搅拌研磨时间。将粉磨12 h后的石英粉在1 000 ml的量筒中进行自由沉降分级,沉降时间为14 h,之后设法收集量筒中悬浮液中的石英微粉,将此石英微粉用纳米粒度与Zeta电位分析仪测定其粒度,粒度微分分布数据见表2。
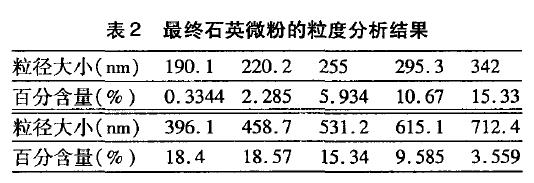
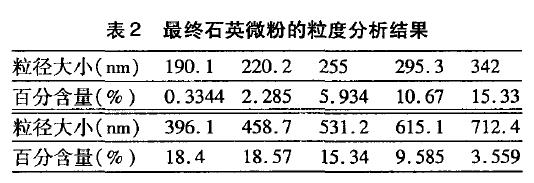
从表2可以看出,用搅拌磨粉磨后再经分级可以制得小于1 I,zm 的石英粉,可满足行业对原料粒度的要求。仪器分析测得粉末的平均粒径为624.7 nm 。
2.4 石英微粉的扫描电子显微镜分析
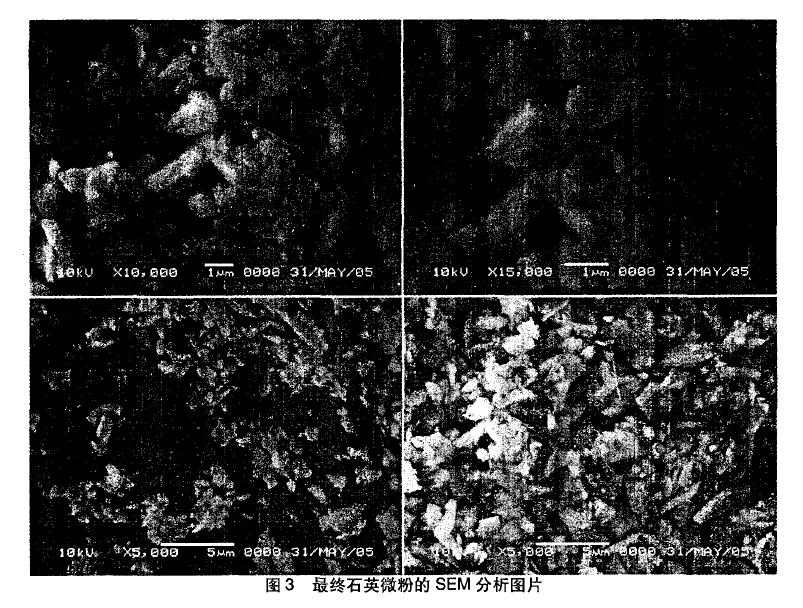
2.4 石英微粉的扫描电子显微镜分析
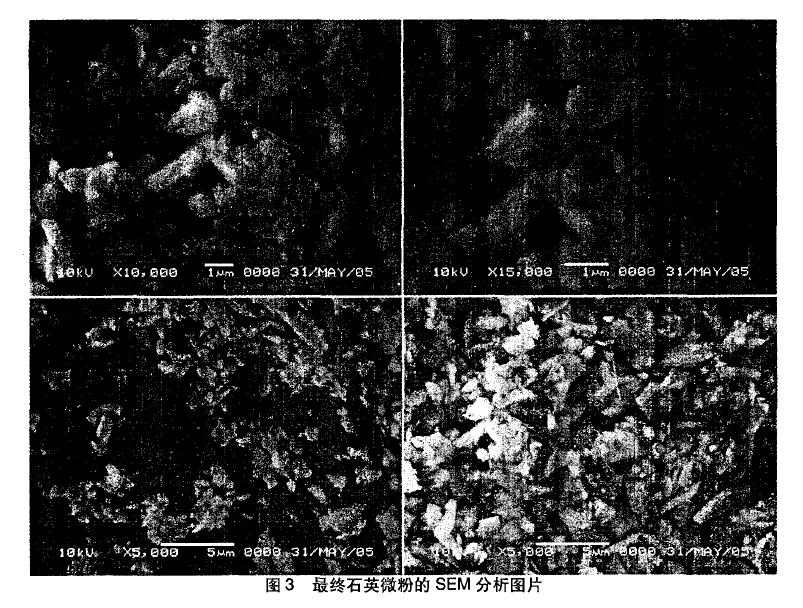
将终石英微粉在扫描电子显微镜下进行形貌观察,照片见图3。由图3可以看出,绝大部分石英微粉的粒径在1 m以下,且多数颗粒形貌一致、均匀,有少数颗粒呈针状,呈球形的颗粒很少。这主要是搅拌球磨机的工作原理主要是粉磨介质球和物料在搅拌器的驱动下作无规则的多维运动和自
转运动,物料在介质球的冲击力、剪切力、研磨力等多种作用力下,不断被粉碎所致,加之石英晶粒力学性能上的多向异性,也可能导致这种现象的发生。
2.5 终石英微粉的化学成分及被污染程度
终石英微粉的化学成分见表3。由表3可知,终石英微粉的SiO:含量可达到99.91% ,其它组分含量很,已达到和超过环氧塑封料等用途的硅微粉要求。终石英微粉被污染的程度小,由于研磨介质球磨损带进的ZrO:占0.0246% ,带进的Y203为0.0014% 。
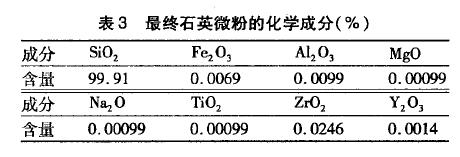
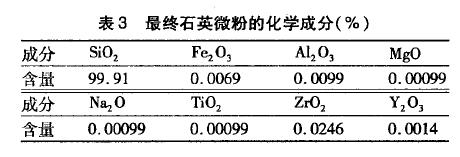
3 结论
(1)用搅拌磨在适当转速、适当磨矿浓度和合适的磨介充填量情况下,经过12 h的粉磨,可获得粒径为1 m以下含量占11.65% 的石英微粉;通过沉降分级可以获取SiO2的含量为99.91% 、1 m以下的石英粉体。不经分级可以获得粒径为61.5 Ixm以下占99.99% 的石英微粉。
(2)用内衬聚氨酯的搅拌磨,以密度为6.0 g/cm 、直径为3 mm的钇稳定氧化锆珠为研磨介质,可将高纯石英砂原料磨细成SiO 的含量为99.9l%的石英微粉,从化学成分和粒度考虑,可达到一般高纯超细硅微粉的质量要求,甚至可达到和超过一般环氧塑封料用硅微粉的要求。
(3)用搅拌磨制备的石英微粉,多数颗粒粒径均匀,但即使粒径小于1 laxn,仍有少数颗粒保持呈石英晶形的长条状,难于获得球形硅微粉。
(4)终石英微粉被污染的程度小,粉磨过程中带进的ZrO 占0.0246% ,带进的Y:O,为0.0014%