行业知识
机械球磨工艺制备超细粒径分散染料的研究
作者:admin日期:2020-07-31阅读
我国分散染料的商品化质量差, 存在着粒径大、粒径的分布范围宽、粒子形状不规则;晶型不清楚;分散稳定性差;能源及原材料消耗高;污染源多,三废治理水平;市场竞争激烈, 规模生产效应已明显下降等忧患[ 1] 。
目前, 国内企业普遍用机械球磨法对分散染料进行后处理加工, 这种方法的优点是产量大、成本、工艺简单。机械球磨法原理是用外部机械的作用, 即通过球磨介质、球磨罐和颗粒的频繁碰撞,颗粒在球磨过程中被地挤压、变形、断裂、焊合。随着球磨过程的延续, 颗粒表面的缺陷密度增
加, 晶粒逐渐细化[ 2] 。
粒径小、分布窄的分散染料颗粒的高温分散性、上染率、提升力等较粒径大的颗粒有明显提高[ 3, 4] 。因此, 要获得粒径小、分布窄的分散染料颗粒, 就必须探讨染料在球磨机中的团聚和破碎机理, 优化球磨工艺。
1 分散染料的团聚和破碎机理
分散染料在球磨机中高速搅拌时, 对于体积V的染料悬浮体体系, 部分体积Veff能克服粒子内部张力, 发生破碎。
假设:在t时, 体系中团聚体的数目为N0 ;在t时, 体系中未破碎的团聚体数目为Nt , 则已破碎的团聚体数目为(N0 -Nt )。在t时, 未被破碎的团聚体N t 受到介质的挤压、剪切、撞击, 将发生破碎。可认为, 在t时, 单位时间内未被破碎的团聚体Nt 发生破碎的数目正比于Nt=Veff/v,比例系数为K1 (与搅拌速度、助溶剂和分散剂等有关)。
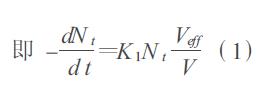
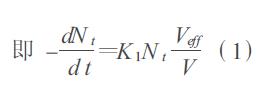
在t时, 已破碎的团聚体数目(N0 -Nt ) 由于颗粒自身的范德华力, 通过热运动将再次团聚。可以认为, 在t时, 单位时间内已破碎的团聚体数目(N0 -N t) 发生团聚的数目正比于(N0 -N t ), 比例系数为K2 (与温度与分散剂等有关)。
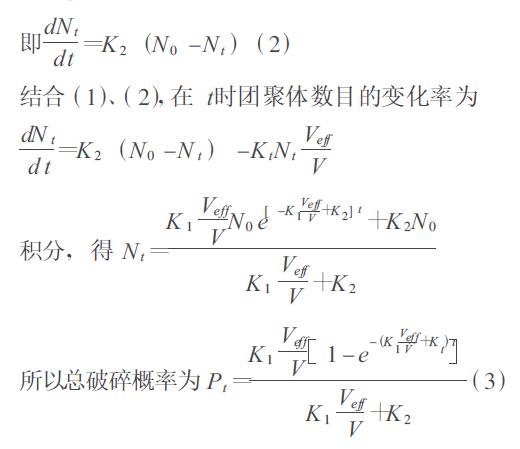
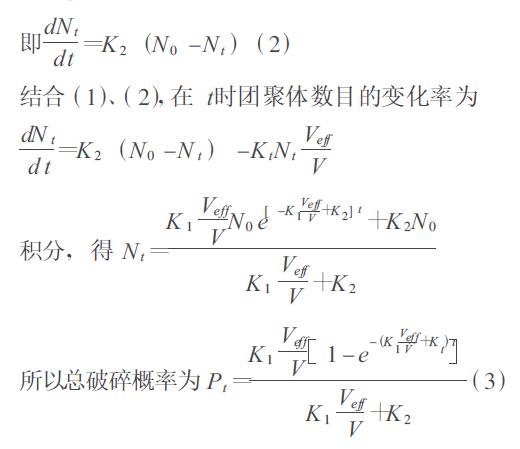
染料破碎概率决定球磨后染料粒径的大小, 破碎概率越大, 团聚数目就越少, 粒径就越小, 反之,粒径就大。
2 实验部分
2.1 实验材料
蒽醌型分散染料滤饼2BLN;分散剂:Reax-85A;木质素磺酸钠AS - 3;分散剂MF;分散剂NK-1;分散剂DK - 2;助溶剂AR。碾磨介质:Υ3 ~5mm玻璃球珠, Υ1mm 玻璃球珠, Υ1mm 氧化锆球。
2.2 实验设备
AX 搅拌球磨机(无锡市海波干燥机械设备厂);MASTER SIZER2000型激光粒度仪(英国马尔文仪器有限公司)。
2.3 实法
选取影响染料研磨的主要参数, 即球磨时间、球磨介质、染料固含量、助溶剂和分散剂, 制定不同的比值, 加入到250mL 的AX 搅拌球磨机中进行球磨, 用MASTER SIZER2000 型激光粒度仪对得到的染料浆液取样分析粒径, 从而得到分散蓝2BLN 的佳工艺参数。
3 结果与讨论
3.1 研磨时间t对粒径的影响
根据理论破碎概率公式(3), 当t由小变大时,Pt 逐渐变大, 但变的越来越慢, 当t接近无穷大时,达到值Pt→∞ , 值为
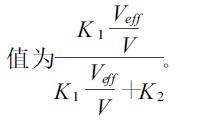
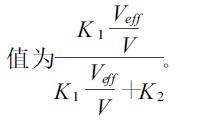
(球磨条件:染料固含量30%, 染料/分散剂=1, 分散剂为Reax- 85A, 染料/研磨介质=1∶20, 研磨介质为 1mm 氧化锆球珠)由图1表明, 在球磨的开始5 小时内, 平均粒径下降速度非常快, 而且粒度分布明显均匀。随着球磨时间增加, 粒径进一步减小的速度非常缓慢,直到12小时后, 染料粒径几乎不变。即随着球磨时间增加, 粒径小的染料相对增加, 达到一定数量
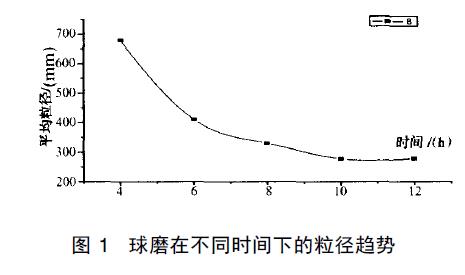
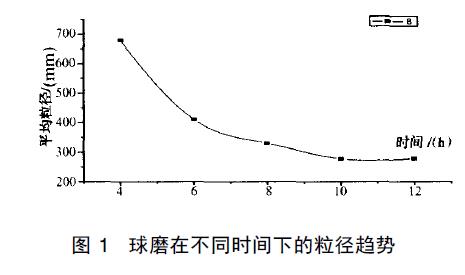
后, 分散和团聚呈现动态的平衡, 此时粒径达到限值, 球磨效率明显下降。但若球磨时间过长, 研磨介质损耗较大, 增加球磨费用, 同时生产效率降。根据实验结果, 实验选用球磨时间为10 ~ 12小时。
3.2 团聚体发生破碎的有效体积Veff的影响
根据理论破碎概率公式(3), 当有效体积Veff越大, 破碎概率就越大。有效体积Ve ff与球磨设备、染料固含量和介质的指标有关[ 2, 7] 。实验室选用AX搅拌球磨机作为染料的球磨设备, 对染料固含量和介质的指标进行了考察。
3.2.1 染料固含量
染料浆液的固含量亦即染料/水比例对砂磨效果有影响, 实验对分散蓝2BLN 在不同固含量下砂磨,其结果如表2所示。
表2 不同固含量下砂磨结果
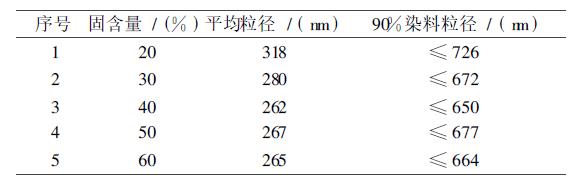
表2 不同固含量下砂磨结果
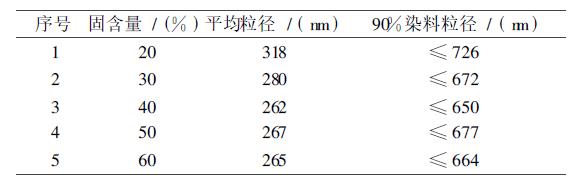
(砂磨条件:染料/分散剂=1, 分散剂用Reax - 85A, 研磨时间12小时, 染料/研磨介质=1∶20, 研磨介质为 1mm 氧化锆球珠)随着染料浆液固含量的增加, 研磨后粒径变小。但到固含量在40%基本达到限。固含量过高后并不会使粒径变得更细, 反使过滤困难, 浆液与研磨介质难以分离。由实验结果得, 固含量在30% ~60%对粒径的影响不大, 因此在实验中均采用30%固含量的染料滤饼。
3.2.2 介质的指标
介质的配比、圆度、密度、直径及填充量都会对破碎概率产生影响, 实验主要研究了介质的直径、密度及填充量对染料粒径的影响。
表3 不同直径的玻璃珠对染料粒径的影响

(球磨条件:染料固含量30%, 染料/分散剂=1, 分散剂用Reax- 85A, 研磨时间12小时, 介质体积均为600m l)
表4 球磨介质对染料粒径的影响
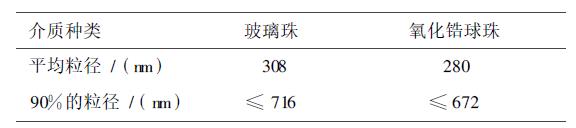
(球磨条件:染料固含量30%, 染料/分散剂=1, 分散剂用Re-ax - 85A, 研磨时间12 小时, 两种介质的直径均为1mm, 体积均为600m l)
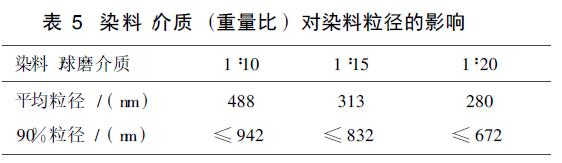
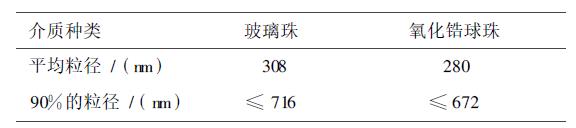
(球磨条件:染料固含量30%, 染料/分散剂=1, 分散剂用Re-ax - 85A, 研磨时间12 小时, 两种介质的直径均为1mm, 体积均为600m l)
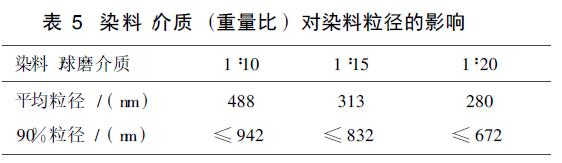
(球磨条件:染料固含量30%, 染料/分散剂=1, 分散剂用Reax- 85A, 研磨介质为 1mm 氧化锆球珠, 球磨时间12 小时)由表3得知, 用直径小的介质球磨后得到粒径更细, 分布更为均匀。若介质过小, 摩擦力会加大而生热, 使已破碎的染料团聚体再次团聚, 降破碎概率, 同时介质过小会给分离带来困难[ 2] 。
由表4可见, 氧化锆珠的球磨效果要好于玻璃珠, 故实验研磨介质均采用氧化锆珠。从表5可见, 染料/介 质的比例对球磨效果影响较大。染料/球磨介质(重量比) 愈小, 其研磨效果愈好, 所得染料粒径愈小。但当介质填充量过多,介质的利用率不高, 且生成热量较多, 易团聚。故实验采用研磨介质为 1mm 氧化锆球, 染料/球 磨介质(重量比) 为1∶20。
3.3 K1 、K2 对粒径的影响
根据理论总破碎概率公式(3), K1 越大, Pt 就越大, 粒径越小, K1 与搅拌速度、助溶剂和分散剂等有关;K2 越小, Pt 就越大, 粒径越小, K2 与温度, 分散剂等有关。
实验时搅拌速度为500 r /m in, 助溶剂选用乙二醇, 球磨时通入冷却水, 并重点考查了分散剂对粒径的影响。
分散染料的分散过程包括三个步骤:湿润、破碎和稳定[ 7, 8] 。且三个步骤都必须用到分散剂, 因此分散剂具有决定性意义, 其具体作用可分为有润湿、分散、稀释、消泡和稳定等。优良的分散剂能显著提高K1 , 并降K2 , 进而提高破碎概率, 降染料的粒径。
实验采用了木质素磺酸盐类分散剂Reax - 85A和AS - 3, 磺化度的萘磺酸类分散剂MF以及高分子分散剂NK -1和DK - 2, 并研究了分散剂对分散染料粒径的影响。
实验发现在分散剂种类的选择上, 分散剂Reax- 85A 和AS - 3 分散效果较好, 这是由于两者都属于木质素磺酸钠分散剂, 这类分散剂除了含有烷基、苯基外, 还含有酚和醇的烃基、甲氧基和羰基等基团, 它们与染料分子不形成范德华力, 而且还可
与染料分子中的氨基、烃基形成氢键, 与染料的结合更为牢固, 使其具有较好的分散稳定性[ 10] 。在染料/分 散剂比例的选择上, 染料/分散剂的比例越少,粒径明显地越细, 而且粒径分布愈均匀。考虑工业化而言, 染料/分散剂比例在1: 0.6 ~ 0.8 较为合适。在分散剂的复配上, 萘磺酸类分散剂MF与木质
素结合使用有利于提高染料粒子的分散稳定性, 从而降染料的粒径。这主要是木质素由于分子大,球磨时不能将染料颗粒完全覆盖, 会存在某些空隙,萘磺酸类由于体积较小, 而使颗粒的表面得到更多覆盖空隙的缘故。
4 结论
分散蓝2BLN的佳球磨工艺参数为:染料固含量为30%, 染料/分 散剂=1:0.6 ~ 0.8 (重量比),分散剂:MF /Reax - 85A =1: 2 (重量比), 助溶剂:乙二醇, 球磨时间为10 ~ 12小时, 研磨设备为AX搅拌球磨机, 研磨介质为 1mm 氧化锆球珠, 染料/介 质=1:20 (重量比)。在上述球磨工艺条件下, 得到了均一稳定的染料液体, 平均粒径为138nm, 90%的粒径小于186nm。