新闻中心
涂料色浆研磨效率的探索
作者:admin日期:2020-02-03阅读
讨论了影响涂料色浆研磨效率的因素,着重研究了研磨设备的工艺参数、研磨介质的类型尺寸、不同的研磨工艺、研磨设备转速和色浆流量对研磨效率的影响。给出了大流量砂磨机在研磨溶剂型涂料色浆时的佳工艺参数:转轴转速为700~800r/min、一道研磨流量为6.5L/min、二道研磨流量为5L/min、以填充比为70%填充Φ1.2~1.4mm纯氧化锆珠,以此工艺参数进行色浆研磨时可以提高研磨效果和研磨效率。
0 前 言
液态色漆,通常由涂料、溶剂、颜(填)料和少量助剂组成。本质上色漆是固体颜料分散在液体涂料中的一种均匀、稳定的分散体。研磨分散设备作为生产色漆的主要设备,起到至关重要的作用[1]。随着汽车涂料等高性能涂料对研磨细度要求不断提高,以及涂料生产企业对生产效率、能耗、等要求的提高,如何通过选用高效率的研磨分散设备、改良研磨工艺、优选研磨介质类型等,达到优化粒径分布、提高分散效率、节能降耗等目的,是涂料生产企业面临的新问题。
1 试验部分
1.1 试验材料
羟基丙烯酸树脂A,工业品,南京;金红石型钛白粉,工业品,四川;酞菁蓝,工业品,南通;中色素炭黑,工业品,邵阳;丙二醇甲醚醋酸酯、S-100A溶剂,工业品,江苏;分散剂,工业品,铜陵。
1.2 试验设备
卧式砂磨机A(重庆);卧式砂磨机B(大流量卧式砂磨机,张家港);刮板细度计(广州)。
本试验采用的砂磨机为卧盘式砂磨机。卧盘式砂磨机研磨腔内介质分布均匀,研磨效率较高,带载启动容易[2]。卧式砂磨机A的结构示意图见图1,卧式砂磨机B的结构示意图见图2。
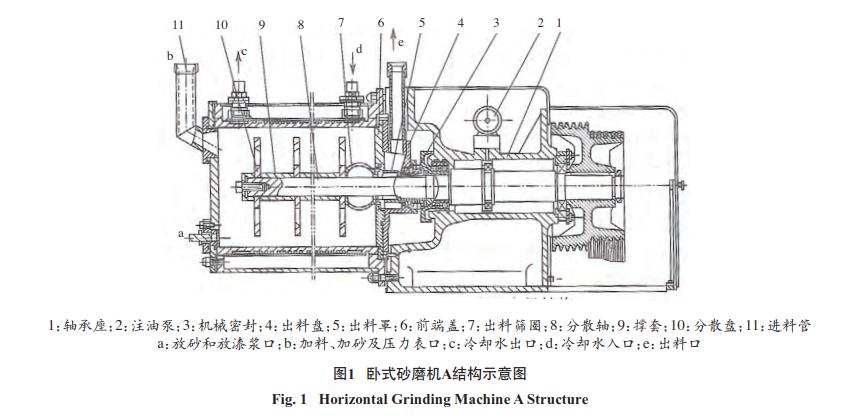
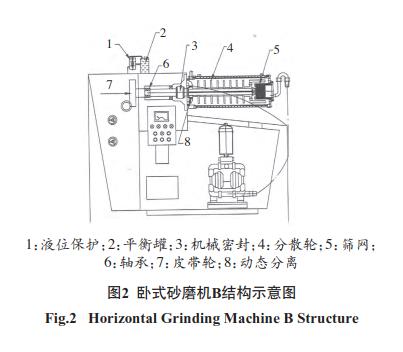
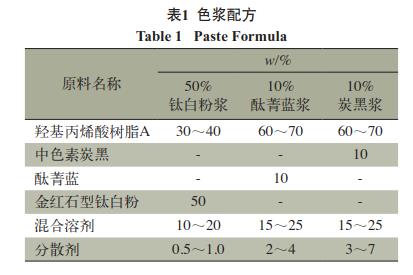
本试验采用的砂磨机为卧盘式砂磨机。卧盘式砂磨机研磨腔内介质分布均匀,研磨效率较高,带载启动容易[2]。卧式砂磨机A的结构示意图见图1,卧式砂磨机B的结构示意图见图2。
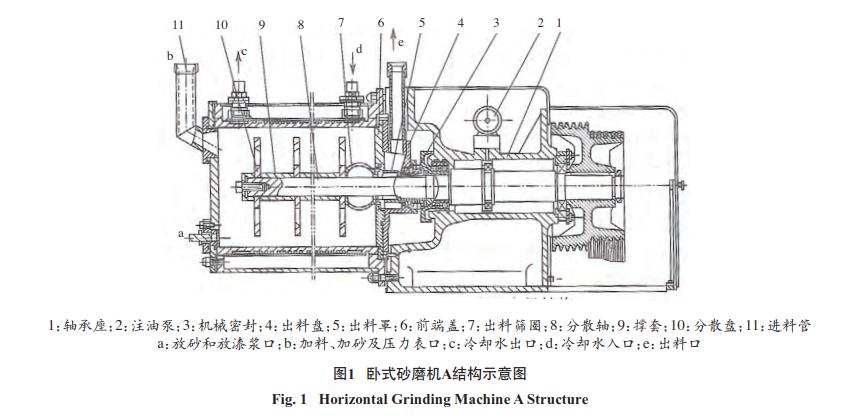
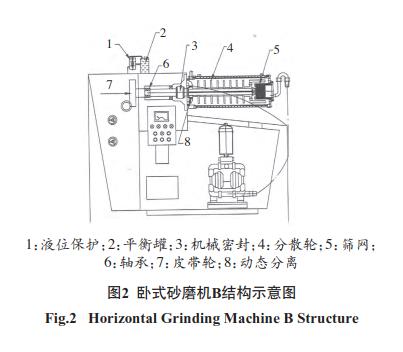
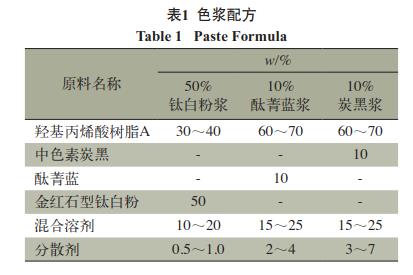
1.3 试法
本试验主要采用羟基丙烯酸树脂A为基料,以金红石型钛白粉、酞菁蓝和中色素炭黑3种颜料进行研磨分散试验,具体色浆见表1。按量制备一定量的色浆,并在分散设备上预分散15min后送至砂磨机进行研磨,每隔一段时间检测细度(中色素炭黑和酞菁蓝在溶剂和分散剂的混合液中浸泡,24h后加入树脂进行预分散)。
2 结果与讨论
2.1 砂磨机参数对分散效率的影响
制备50%钛白粉浆450kg,10%酞菁蓝浆250kg,10%炭黑浆250kg,分别在卧式砂磨机A和B上进行研磨,每隔一段时间用刮板细度计测量细度,考察不同砂磨机参数、分离方式类型对分散效率的影响,砂磨机参数对比见表2,试验结果见图3~图5。
由表2可知,卧盘式砂磨机B与A相比,容积小,其 密度(功率/容积)大,可以采用密度和硬度更大的纯氧化锆珠来提高研磨效果,且更小的容积在颜色转换时的损耗也相对较小,降了色浆研磨的消耗成本。
B型砂磨机的分离器结构为转子动态分离筒式结构(见图6),可以采用粒径更小的研磨介质且不会堵塞筛网。介质分离模式的改变是砂磨机发展中的重要技术革新。A型传统砂磨机使用的缝隙环过流面积小,在使用小尺寸的研磨介质时,由于筛网是静态结构,容易发生堵塞;而正常尺寸的研磨介质因磨耗变小,鼓型缝隙环因长期磨损,导致缝隙尺寸变大,也容易发生研磨介质卡在缝隙环中的现象,导致流量降。B型卧式砂磨机使用的是动态离心分离系统,分离转子带动介质旋转而产生的离心力使介质被甩向转子外周围,而转子中心主要是色浆,分离筛网布置在转子中心,色浆可以顺利通过筛网缝隙而流出,不易发生堵塞及磨损,保证了色浆分离的稳定性。
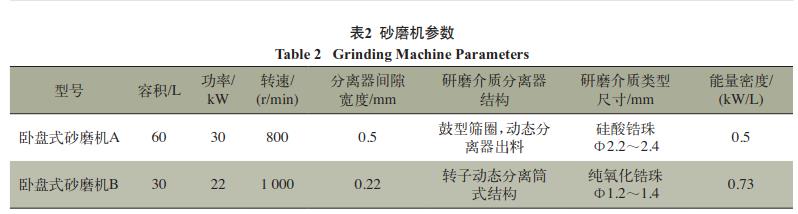
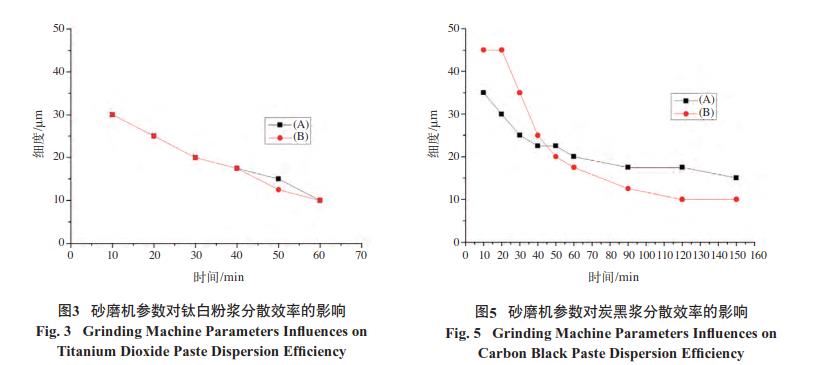
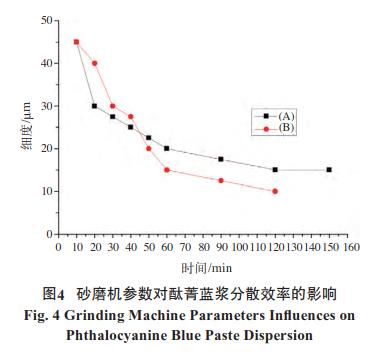
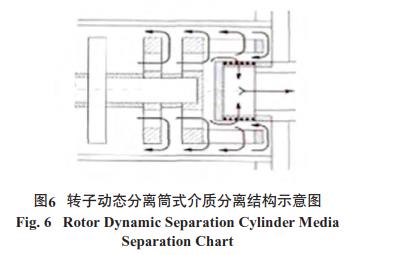
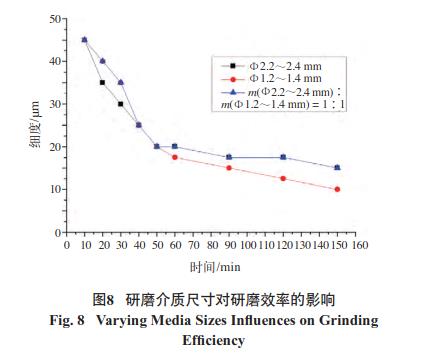
2.3 研磨工艺对研磨效率的影响
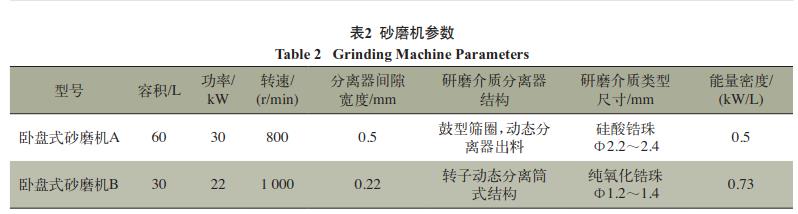
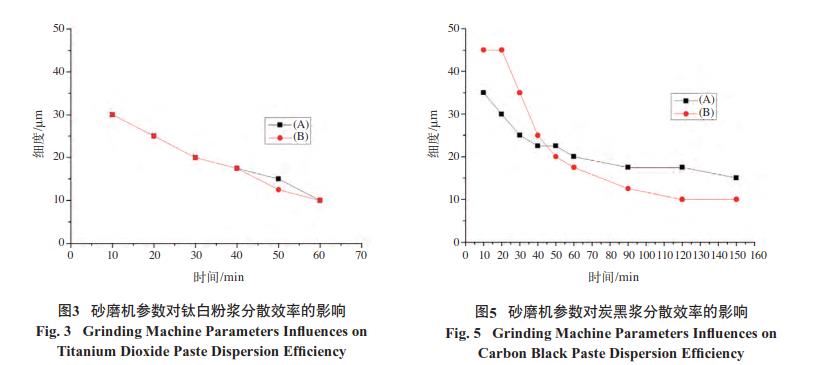
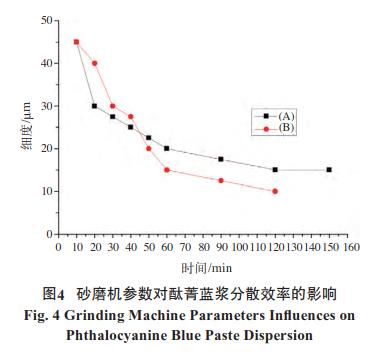
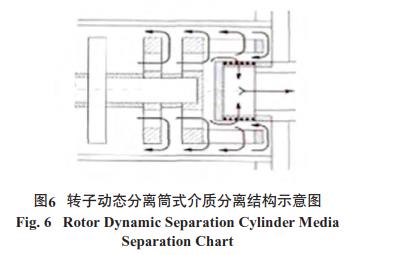
由图3~图5中的时间-细度曲线可知,对于较容 易分散的钛白粉等无机颜料,两种砂磨机在分散效率上差别较小,对较难分散的酞菁蓝等颜料和炭黑等,在分散初期(0~30min)A型砂磨机的分散效率更高,细度降得更快。这是由于在研磨初期浆料颗粒较大、数目多,冲撞、挤压作用占主导,大部分是把颗粒料碰撞为很多碎片,而根据动力学公式P=mv可知,研磨介质的动能P在线速度v相近的情况下,与研磨介质的质量m成正比。A型砂磨机采用的Φ2.2~2.4mm的硅酸锆珠具有更大的质量,动能更大,对撞击作用的贡献更大。而在30min后,随着浆料细度的下降,粒径小的研磨介质在相同体积下的接触多,研磨效率比A型砂磨机高;而B型砂磨机也因为设备具有较高的密度和尺寸更小、密度更大的研磨介质,在色浆的终分散细度上优于A型砂磨机。
2.2 研磨介质对色浆研磨效率的影响
2.2.1 研磨介质的类型对研磨效率的影响
研磨介质按材料不同可以分为玻璃珠、陶瓷珠(包括硅酸锆珠、二氧化锆珠)、钢珠等。
化学组成及制造工艺的差异决定研磨介质的晶体结构的不同,继而决定了研磨介质不同的抗压强度和耐磨性,成分的含量不同决定了研磨介质的密度,而由动力学公式P=mv可知,研磨介质的冲量P与研磨介质的质量成正比,研磨介质的密度越大,动能越大,研磨效率也就越高[3]。
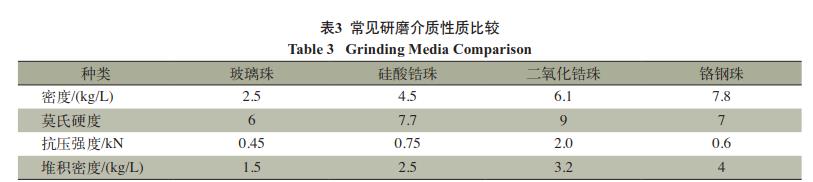
配制450kg的钛白粉浆,在A型砂磨机中按65%体积填充比分别填充玻璃珠(Φ2~3mm)和硅酸锆珠(Φ2.2~2.4mm),在额定功率下研磨,每隔一段时间测定细度,试验结果见图7。
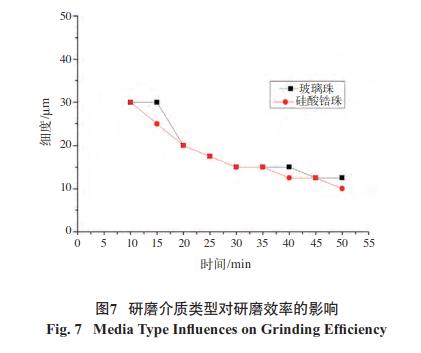
由图7可知,硅酸锆珠的分散效率略高于玻璃珠,这主要是由于在硅酸锆珠相比玻璃珠的堆积密度和硬度大,具有更高的动能,提高了研磨效率;而在实际生产过程中也发现,相比硅酸锆珠,玻璃珠的磨耗率更高,更容易出现碎珠现象,卡在介质分离的缝隙内,阻塞出料装置,影响研磨效率。
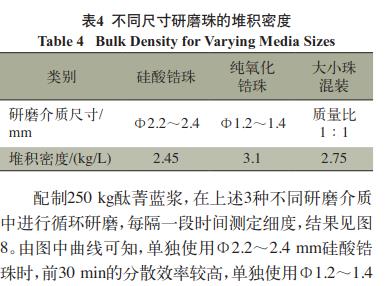
配制250kg酞菁蓝浆,在上述3种不同研磨介质中进行研磨,每隔一段时间测定细度,结果见图8。由图中曲线可知,单独使用Φ2.2~2.4mm硅酸锆珠时,前30min的分散效率较高,单独使用Φ1.2~1.4mm氧化锆珠时,产品终细度,采用大小珠混合的方式时,效率并没有比单独使用Φ1.2~1.4mm的研磨介质提高,反而有所降。
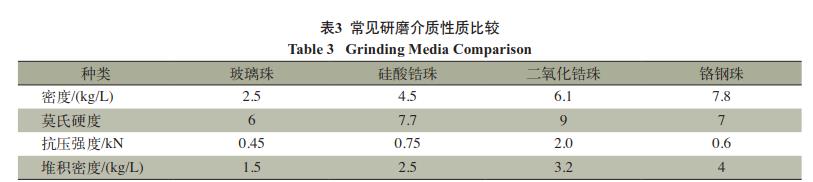
配制450kg的钛白粉浆,在A型砂磨机中按65%体积填充比分别填充玻璃珠(Φ2~3mm)和硅酸锆珠(Φ2.2~2.4mm),在额定功率下研磨,每隔一段时间测定细度,试验结果见图7。
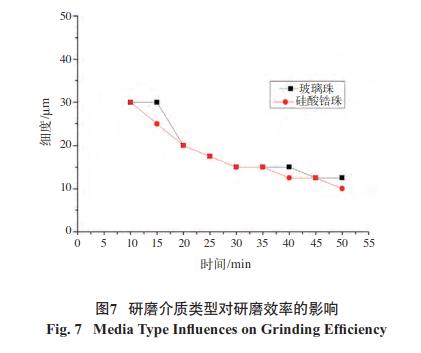
由图7可知,硅酸锆珠的分散效率略高于玻璃珠,这主要是由于在硅酸锆珠相比玻璃珠的堆积密度和硬度大,具有更高的动能,提高了研磨效率;而在实际生产过程中也发现,相比硅酸锆珠,玻璃珠的磨耗率更高,更容易出现碎珠现象,卡在介质分离的缝隙内,阻塞出料装置,影响研磨效率。
2.2.2 研磨介质的尺寸对研磨效率的影响
研磨介质的大小决定了研磨介质与色浆的接触点的多少,粒径小的研磨介质在相同体积下的接触点越多,理论上的研磨效率越高;但另一方面,在研磨初期颜料粒径较大时,研磨介质粒径小的冲量较小,达不到较好的研磨效果;研磨后期,大粒径的研磨介质由于接触点少,密度不足,导致粒径分布比小尺寸研磨介质差[4]。
本试验结合廖红[5]等在砂磨机研磨介质装填量中的计算和笔者的实际应用经验,在卧盘式砂磨机B中按70%体积填充比分别填充Φ2.2~2.4mm硅酸锆珠、Φ1.2~1.4mm纯氧化锆珠和上述两种研磨介质按质量比1∶1混装的混合珠,分别测定堆积密度,结果见表4。
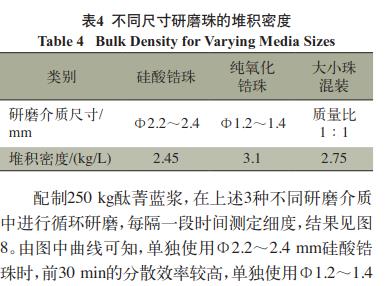
配制250kg酞菁蓝浆,在上述3种不同研磨介质中进行研磨,每隔一段时间测定细度,结果见图8。由图中曲线可知,单独使用Φ2.2~2.4mm硅酸锆珠时,前30min的分散效率较高,单独使用Φ1.2~1.4mm氧化锆珠时,产品终细度,采用大小珠混合的方式时,效率并没有比单独使用Φ1.2~1.4mm的研磨介质提高,反而有所降。
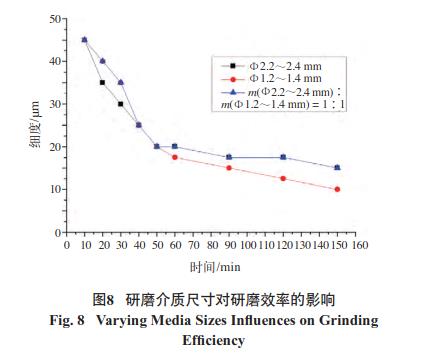
2.3 研磨工艺对研磨效率的影响
不同品种的色浆,因其颜料类型(无机颜料、颜料、炭黑)、细度要求、色浆黏度等参数的不同,所对应的研磨工艺也不尽相同。选择合适的色浆研磨工艺可以显著地提高色浆的研磨效率,提高色浆的研磨效果,对产量的稳定性提高有非常重要的意义。
按量制备250kg炭黑浆,采取3种不同的研磨工艺进行研磨,并分别测定细度如下:
(1)卧砂A单机双缸三道,细度达到17.5μm;(2)卧砂B单机双缸三道,细度达到12.5μm;(3)卧砂A一道+卧砂B二道,细度达到10μm。
结果表明:(3)卧砂A一道+卧砂B二道的模式,结合了A型砂磨机前期效率高和B型砂磨机后期效率高、终细度的特点,提高了分散效率。在实际生产中使用该工艺一段时间后统计,研磨中色素炭黑和颜料色浆时,研磨效率提高15%以上,且色浆拥有贮存稳定性。
2.4 色浆流量对研磨效率的影响
用卧式砂磨机B(大流量卧式砂磨机)进行试验。以70%填充比填充Φ1.2~1.4mm纯氧化锆珠,相同的转轴速度(800r/min)和同一冷却水条件下,对比不同色浆流量对研磨效率的影响,试验结果见表5。
由表5可知,在相同的转轴速度下,选择大流量时,色浆在筒体内的停留时间短,在无机颜料的分散和颜料的初期分散中,细度相差不大,而分散颜料的后期,适当降流量,增加在筒体内的停留时间,可以保证通过两次研磨即可达到细度要求,
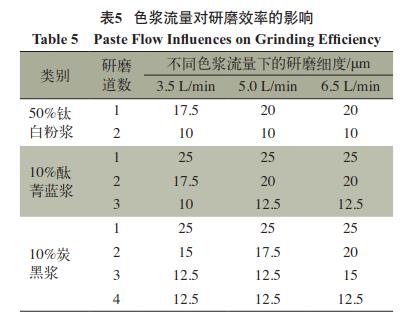
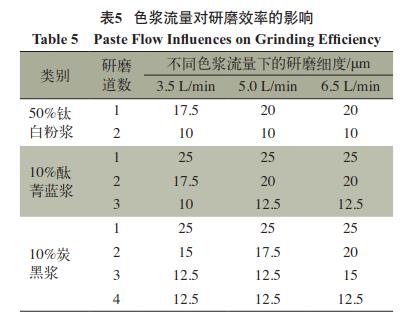
减少了研磨道数。因此选择一道色浆流量为6.5L/min,二道色浆流量无机颜料6.5L/min、颜料和炭黑色浆为5L/min。
3 结 语
(1)涂料色浆的研磨效率和效果与研磨分散设备的参数、研磨介质类型与尺寸和研磨工艺有关;研磨设备介质分离结构的动态离心分离系统比传统的鼓型出料筛圈在介质分离的稳定性上有优势;采用填充卧式砂磨机A(Φ2.2~2.4mm硅酸锆珠填充)串联卧式砂磨机B(Φ1.2~1.4mm纯氧化锆珠填充)的研磨工艺,提高了羟基丙烯酸树脂色浆的研磨效果和稳定性,研磨效率提高15%以上。
(2)大流量卧式砂磨机拥有高密度和动态介质分离结构的设计特点,实现了较好的研磨效果和较高的研磨效率。选择6.5L/min为一道研磨流量,5L/min为二道研磨流量,以填充比为70%填充Φ1.2~1.4mm纯氧化锆珠的设备运行参数和工艺,研磨效果较好,可以提高色浆的研磨效率。