行业知识
悬浮剂加工方法和砂磨技术
作者:admin日期:2020-06-11阅读
砂磨技术
目前国内采用湿式砂磨技术生产悬浮剂的工艺颇为成熟,但市场上见到的悬浮剂产品良莠不齐。有很多悬浮剂产品存放一段时间后产生分层、析水和沉淀,甚至于个别产品存在严重结底问题,不易搅动和倒出,致使用户使用不便,降药效和浪费药液。
实际上,在研发得到悬浮剂优后,需要进行产业化;对于砂磨技术实施的好坏,就会直接对生产的悬浮剂产量产生重大影响。
1.砂磨设备
砂磨设备从一台使用粒径较大的砂磨球的搅拌式球磨机(Attri-tor)诞生,已经发展到使用粒径较小的研磨珠的砂磨机。自1948年美国杜邦公司发明立式砂磨机后,其结构经过了不断改革,1952年起在颜料和油漆行业得到广泛应用,在国内约70%~80%涂料产品是由砂磨机完成的,以后进入到加工领域。
由于加工的固体活性成分大多为毒性大、粘度高、研磨时易起泡的物料,以后发展到使用密闭卧式砂磨机,其中尤以瑞士DynomillR和比利时的SupermillR使用较多和效果好,但价格相对较贵。使用的瑞士DynomillR卧式砂磨机,是一种水平湿式连续性生产的超微分散机。它运转功能是利用泵将预先混合搅拌好的物料送入到主机的研磨槽,槽内填充适量的研磨介质(如玻璃珠和锆珠等),经由分散叶片高速转动提供研磨介质足够的动能,与被分散的颗粒冲击产生剪切力,达到高的分散效率;再经由特殊的分离装置,将被分散物与研磨介质分离排出。这种卧式砂磨机质量上乘、性能可靠、效率高,在欧美等发达受到青睐。随着砂磨机的不断改进,已出现了双锥砂磨机(意大利)和纳米砂磨机等新型卧式砂磨机。卧式砂磨机优点是:具有精细研磨的功能,采用特殊材料加工筒体和分散盘耐磨性和耐腐蚀性好,同时可消除设备对浅色物变色污染;全密封结构减少有害物料的挥发和对操作者伤害,有利于周围环境保护。
加工的物料粒度分布均匀、有效物料干枯和结皮、操作和清洗方便简单;同时噪音小、效率高、生产量大。
之后又出现一种改良功能的超细研磨的新一代砂磨机,例如CentexR全容积珠磨机、瑞士布勒有限公司(BuhlerAG)产品。该类砂磨设备具有瘦长型的更小研磨腔,形成许多连续的研磨单元,使得研磨珠的运动更加有力;从研磨料入口到反射笼间各个尺寸有一致的研磨单元,使得研磨腔有效容积得到大的利用,同时拥有较大直径的中性和传递作用的EcoMizerR高效研磨盘片,了研磨珠在局部堆积,使得流量更高,保证了在更的转速下仍能有小地提高研磨珠的撞击力,使得研磨更加经济。
目前国内外普遍使用卧式砂磨机生产悬浮剂产品;密闭卧式砂磨机比立式砂磨机能力可提高近2倍,起动功率,消耗小,更深受用户青睐。
在悬浮剂加工中,砂磨机是分散工序中重要的设备,其主要功能是将固态粒子分散于液体介质(水)中。一般砂磨功能实际上包括三个阶段:
(1)湿润(wetting),固态粒子表面所吸附的气体被液体所取代。
(2)研磨(grinding),将大粒子研磨成小粒子,同时将凝集的颗粒粒子利用机械力碎裂成原始粒子。
(3)分散(dispersion),将已湿润过的原始粒子移入液体介质(悬浮在液体内)而产生持久的粒子分离。
卧式砂磨机运转工艺是:物料在容器中充分混合搅拌(通过高剪切)均匀后,由送料泵将预先混合搅拌好的物料以一定流量速度送入卧式砂磨机机身筒体内的研磨槽,槽内填充适量的研磨介质(如玻璃珠和锆珠等),经由电动机通过带动分散盘作高速运转,
分散盘叶片带动研磨介质运动提供足够的动能,而与被分散的颗粒冲撞产生剪切力和摩擦力,使物料颗粒得以研磨和分散,大颗粒研磨成较小颗粒,终使粒度大小不一的物料颗粒变为所需粒度均匀的小微粒,达到高的分散效率。再经由特殊的分离装置,将被分散物与研磨介质分离,研磨后料再由出料口流出,进入下一步工序。
加工悬浮剂的各种混合物料通过砂磨机的研磨,要达到一定细度和粘度以及粒度分布均匀的悬浮率高的产品。
通过实践和经验表明,通常需要经过2~3次研磨,物料平均粒径可以达到2~3μm。具体操作方法是采用多台砂磨机串联使用,每台砂磨机筒体中使用的研磨介质粒径可以是相同的或者不同的;倘若是不同的,通常排列顺序是研磨介质粒径是由粗到细。
除了变换研磨介质粒径大小之外,也可通过延长筒体中物料的研磨时间(即降进料流量),使研磨介质产生的剪切力和摩擦力得以充分发挥,同样达到降物料粒径的目的。
2.影响砂磨效率的因素
(1)的含固率
含固率指悬浮剂中含有固体成分的比例。当通过湿粉碎把和助剂等物料制成浆料后进行研磨粉碎时,若含固率太,单位体积浆料中颗粒少,介质研磨的机会少,这时研磨效率反而会降;如含固率过高,使之间的内摩擦加剧,介质研磨的机会增多,研磨效率提高,但能耗也会增加。因此,一般要求是在具有一定的流动性情况下,含固率尽可能高是有利的。
(2)原药的粒径
因砂磨机结构的因素,对大颗粒的粉碎效率是不高的,若进入砂磨机的粒径小于320目(或43μm)时,研磨效率则会明显提高。因此,对有大颗粒或结块的原药可通过预粉碎,使颗粒粒径小于320目(或43μm)后进入砂磨机,可大大有效提高砂磨机的生产能力和效率。
(3)研磨室容积
砂磨机的生产能力与研磨室容积并非是成正比的,日本五十岚机械株式会社试验结果表明,砂磨机研磨室容积在2~30L之间,生产能力与研磨室容积是成正比的。而在60L以上情况有所不同,实际生产情况与理论值相差较大,生产效率随研磨室容积的而下降。
五、研磨介质对磨效的影响
早期的研磨介质是用渥太华砂制成的,但一般是不圆和易碎的。以后出现各种人造的微球(珠),现在大多数研磨介质都采用人造材料(可选用多种材料)制成的。
1.研磨介质的作用
研磨介质的球形体在砂磨机内随分散叶片运转的同时,其本身也就会产生自转动能。其总动能可以用如下公式表示:T=1/2mv2+1/2Jω2。
式中T为研磨介质的总动能,m为研磨介质的质量,v为研磨介质的运动速度,J为转动惯量,ω为研磨介质运动的角速度。从式中可见,前一项为研磨介质的质量运动时带来的动能;而后一项为研磨介质自转产生的动能,由此提供了对物料颗粒的摩擦和剪切力,起到对颗粒的粉碎和破裂作用。显然自转的角速度越大,产生的自转运动能也越大;倘若研磨介质的球形体不均匀时,
自转运动受阻时,会降自转运动能,对研磨是不利的。
2.研磨介质的类型一般研磨介质有玻璃珠、石珠、锆珠和钢珠等,但使用多的为玻璃珠和锆珠。可依据研磨物料的理化性质和研磨难易程度进行选择。表7和表8分别列出研磨介质的某些性质。
对于国内进口的Dyno-MillR卧式砂磨机,通常使用国外进口的玻璃珠NanorSiR,比国产的玻璃珠各项性能(强度、耐磨度、球型圆整度等)好。这种玻璃珠采用直接熔化滴定、去离子水中成型、高温硬化和抛光等先进加工技术制成的,球型度高达,球内绝无气泡,具有优异的耐磨性。这种玻璃珠适用于粘度(600~1800mPa·s)的分散和研磨;而悬浮剂产品控制的加工粘度通常在300~1200mPa·s之间,所以国外用Dyno-Mill卧式砂磨机加工的悬浮剂中都使用玻璃珠,而很少使用锆珠。因为锆珠适用的粘度较高,例如1000~3500mPa·s,可选用硅酸锆珠;2300~5000mPa·s,可选用或的纯锆珠。
国内可使用的锆珠(主要成分为95%ZrO2+5%Y2O3,直径分别为0.4~0.6、1.0~1.2、1.8~2.0mm)其参数为示于表9。
为了在使用NanorSiR玻璃珠作研磨介质避免珠子的破碎和磨损过大,要求做到以下几点:
一是珠子的填充量不要超过上限(85%);
二是不同材料的珠子不能混用;三是尽量使用粒径均一的珠子;四是当带珠子清洗砂磨机时应该保持转速(小于100r/min),机械调速的砂磨机采用点动;五是定期筛去破碎的旧珠子;六是定期检查砂磨机分离装置出料端盖和分离轴的位置等是否有裂口或凹槽。
一是珠子的填充量不要超过上限(85%);
二是不同材料的珠子不能混用;三是尽量使用粒径均一的珠子;四是当带珠子清洗砂磨机时应该保持转速(小于100r/min),机械调速的砂磨机采用点动;五是定期筛去破碎的旧珠子;六是定期检查砂磨机分离装置出料端盖和分离轴的位置等是否有裂口或凹槽。
当使用锆珠作研磨介质的卧式砂磨机,对卧式砂磨机的砂磨筒体材质有很高要求,一般都选用高硬度的合金钢作材料,这样才能经得起锆珠的研磨。
在使用中,并不是每种悬浮剂品种都要用锆珠,那些原药本身是难以砂磨的结晶体,或者制备高浓度悬浮剂时才使用,一般效果较好,砂磨时间要比用玻璃珠的节省1/3~1/2。
国内生产悬浮剂选用国内或国外的密闭卧式砂磨机产品,要看每个公司的能力及生产的品种而定。
3.研磨介质直径的选择
物料的研磨是通过研磨介质之间的接触,产生挤压和剪切的粉碎物料的机械力进行的。在两个研磨介质接触后,形成一个接触区,只要进入研磨介质的球体间接触区(区),才有可能被粉碎。
研磨区域以如下公式表示:Va=2r(2R+1/3r)。
式中:Va为有效区域,R为研磨介质半径,r为物料半径。就单位体积而言,小研磨介质比大研磨介质的区域了约1/R2。假如随机堆积因素φ=0.639,每个研磨介质有4.6个接触点。
在25.4mm(3相当于1in3)的体积中,研磨介质直径为3.1754mm(1/8in)有2900个接触点;而研磨介质直径为0.794mm(1/32in)有180000个接触点,即小研磨介质直径是大研磨介质直径1/4时,接触点约62倍,这是小研磨介质提高研磨效率的主要原因。
因此,如果加入相同体积的研磨介质,小研磨介质比大研磨介质的研磨效率要高,因为小直径比大直径的研磨介质的区要大。试验也证明,分别用1mm和2mm在200ml的微型砂磨机研磨物料(如除草剂),研磨到同一粒径的时间分别为3h和7h。
再如某一种牌号的粒径为2mm硅酸锆珠,每升约使用20000颗;而粒径为1mm硅酸锆珠,每升约使用约
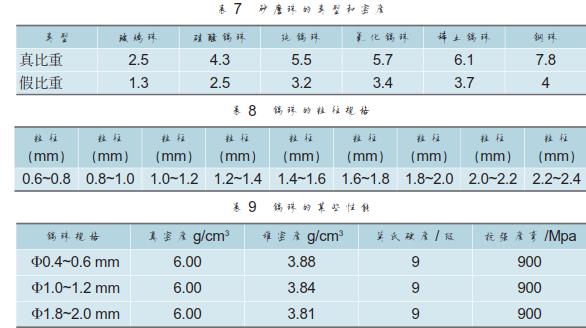
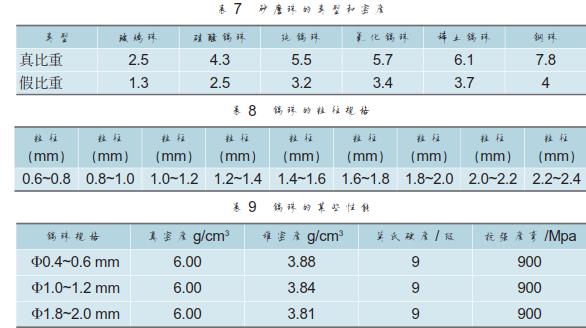
该保持转速(小于100r/min),机械调速的砂磨机采用点动;五是定期筛去破碎的旧珠子;六是定期检查砂磨机分离装置出料端盖和分离轴的位置等是否有裂口或凹槽。
当使用锆珠作研磨介质的卧式砂磨机,对卧式砂磨机的砂磨筒体材质有很高要求,一般都选用高硬度的合金钢作材料,这样才能经得起锆珠的研磨。
在使用中,并不是每种悬浮剂品种都要用锆珠,那些原药本身是难以砂磨的结晶体,或者制备高浓度悬浮剂时才使用,一般效果较好,砂磨时间要比用玻璃珠的节省1/3~1/2。
国内生产悬浮剂选用国内或国外的密闭卧式砂磨机产品,要看每个公司的能力及生产的品种而定。
3.研磨介质直径的选择
物料的研磨是通过研磨介质之间
的接触,产生挤压和剪切的粉碎物料的机械力进行的。在两个研磨介质接触后,形成一个接触区,只要进入研磨介质的球体间接触区(区),才有可能被粉碎。
研磨区域以如下公式表示:Va=2r(2R+1/3r)。
式中:Va为有效区域,R为研磨介质半径,r为物料半径。就单位体积而言,小研磨介质比大研磨介质的区域了约1/R2。假如随机堆积因素φ=0.639,每个研磨介质有4.6个接触点。
在25.4mm(3相当于1in3)的体积中,研磨介质直径为3.1754mm(1/8in)有2900个接触点;而研磨介质直径为0.794mm(1/32in)有180000个接触点,即小研磨介质直径是大研磨介质直径1/4时,接触点约62倍,这是小研磨介质提高研磨效率的主要原因。
因此,如果加入相同体积的研磨介质,小研磨介质比大研磨介质的研磨效率要高,因为小直径比大直径的研磨介质的区要大。试验也证明,分别用1mm和2mm在200ml的微型砂磨机研磨物料(如除草剂),研磨到同一粒径的时间分别为3h和7h。
再如某一种牌号的粒径为2mm硅酸锆珠,每升约使用20000颗;而粒径为1mm硅酸锆珠,每升约使用约80000颗,后者是前者的4倍。使用较大粒径锆珠对某一产品进行研磨时,无论经过多少次砂磨,物料的粒径始终未能达到要求的细度;而改用粒径较小的研磨珠时,效果即得到明显的提高。
允许使用的小研磨珠粒径已经成为衡量砂磨机质量档次的一个重要指标,研磨机的分离装置的改进也使得使用超细研磨珠成为可能。分离装置设计和制作材料的每一次改进,都给使用更小的研磨珠颗粒带来不小的飞跃。
分离装置从传统静止扁平的Nick-el网到带三角横梁的Johnson网,已发展到动态的环式分离器和套筒式Cartridge网,这种改进除了导致使用寿命延长之外,也能使使用的研磨介质的粒径越来越小,而同时又不会明显影响物料的流量。如美国的PremierR的速宝磨,使用套筒式Cartridge网的小珠子粒径达到0.2mm;而瑞士的Dyno-millR实验室型使用环式分离器,
可用的珠子粒径也可达到0.2mm。而瑞士布勒(Buhler)公司研制的离心式分离装置,分离原理从区分珠子粒径大小转为区分珠子密度大小,将研磨珠得到小粒径推向新的限。
但是也应该看到,过小的直径(如0.5mm以下),因摩擦产生的热量也多,会使浆料升温达到一定温度,不利于研磨,研磨效率反而降。这时必需采取措施以加大冷却效果,如增加冷却流量或者降冷却介质的温度。因此,通常使用的砂磨机,一般认为使用的研磨介质直径约在1~2mm之间。有效;而过去曾使用的砂磨锅(现在一般都不用了),其使用的研磨介质的直径一般在3~5mm左右。
4.研磨介质的均匀度
通常地有两种看法:
一是从动力学角度考虑,研磨介质的直径尽可能一致时,体积相同,则质量(m1=m2)相等。这时两个等直径的研磨介质可以获得相同的动能(m1v1=m2v2),相碰时产生相同的挤压力和剪切力;如两种不等直径的球,(m1>m2时,则m1v1>m2v2),两球相碰时会造成大球追小球情况,研磨效率反而会下降。
二是从几何学上来考虑,大小球混装,小球可填充至大球的空隙中,增多了研磨介质的接触点,因而可以提高研磨效率。德国DRAIS公司可能出于这一个原因,曾认同不同直径研磨介质球混装。但笔者认为,采用大小球混装,在研磨开始时,当浆料中有团块和大块颗粒时,需要较大相碰的挤压力和剪切力,大的研磨介质可提供较大,这时是有利的。当进入微细研磨阶段时,直径小的研磨介质更能起到研磨作用,而直径大的研磨介质,反而会出现大球追小球现象,反而使研磨效率有所下降。目前研磨珠的直径偏差愈来愈小,对于砂磨机而言,均匀度好的研磨珠,不对粉碎物料细度的狭窄分布有一定好处,而且可大为减少碎珠的产生,进而减少砂磨机接触件的磨损,同时也避免对产品的污染。目前市场上使用的研磨介质粒径偏差可保持在0.1mm。均匀的研磨珠因制作工艺复杂,所以市场价格也相对较高。
5.研磨介质的比重(或密度)
通用的研磨珠如玻璃珠、石珠、硅酸锆珠、氧化锆珠(纯锆珠)和铬钢珠的比重是依次递增的,而它们的硬度、抗压强度和耐磨性除了铬钢珠外,也是依次的,见表10所示。
对同一种浆料,研磨介质的比重不同,研磨效率也不同。从动力学公式P=mv可知,珠子的冲量P与珠子的质量m成正比,密度大的珠子运动能力越大,一般研磨效率也越高。但对使用在悬浮剂加工中,事实并非如此,
比重大的研磨介质容易沉积到研磨室底部,介质之间的接触点减少,研磨效率反而降;另一方面,比重大的研磨
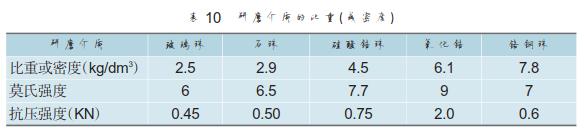
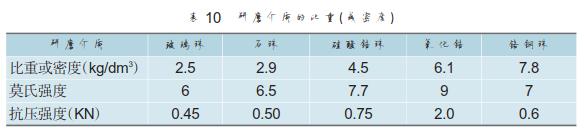
介质消耗也越大,研磨介质的机械能转化为大量的使浆料温度升高,从而加剧了微小粒子的布朗运动,造成已磨碎的颗粒重新凝聚。一般研磨介质的比重与浆料的粘度应该相适应为好,即高粘度浆料选用比重大的研磨介质,反之选用比重小的研磨介质。一般选用比重超过3的研磨介质,容易沉积到研磨室底部,研磨效率将会下降,用陶瓷珠与玻璃珠进行对比试验时也证明这一点。
6.研磨介质的填充率
研磨介质填充率的高对研磨效率影响较大。当填充率过大时,研磨过程中容易产生较多热量,使浆料升温过快,热运动加剧,使得已研碎的物料又重新团聚,研磨效率反而降。一般来说,填充率装填有一定的范围,通常为50%~80%为宜。过高时也会加速研磨设备的磨损,过则延长研磨时间,甚至达不到研磨所需粒径。除此之外,填充率与研磨浆料的粘度也有一定关系,一般浆料的粘度较时,可采用填充率范围的下限(50%~60%);反之,浆料的粘度较高时,可采用填充率范围的上限(70%~80%)。
7.研磨介质的耐磨性
研磨介质的耐磨性也是衡量研磨介质好坏的一个重要条件。不耐磨的研磨介质(如玻璃珠和陶瓷珠),因磨损而需要经常进行补充和更换,不增加了成本,而且也会影响正常生产。磨耗的研磨介质除了会影响产品的质量之外,同时还会对机械部件如叶片、筒体、料泵及密封都带来危害,因此在选用研磨介质时应该特别要考虑其耐磨性。在研磨介质的耐磨性试验中,研磨某种浆料时,玻璃珠在100h内磨损率为0%,陶瓷珠磨损率为1.8%,表明玻璃珠比陶瓷珠的耐磨性要好;而研磨介质锆珠则可以使磨损率减少至1/10000以下,是耐磨性好的研磨介质。
六、研磨转速的影响
砂磨机对物料进行砂磨时,研磨转速对研磨效率也有影响。在研发某悬浮剂小试验砂磨设备中,可以看到如下情况:通常在条件不变情况下,较的研磨转速(如1000r/min)得到悬浮剂粒径较大(D50为5.5μm),增加研磨转速到1500r/min,其D50值迅速降到1.3μm;随着研磨转速增加到2000r/min,其D50值降已不明显(1.2μm)。当继续增加研磨转速到2500r/min、3000r/min、3500r/min时,发现虽然物料被研磨粉碎的速度加快,但粒径基本保持稳定D50值(1.18μm),其原因是当研磨转速达到一定值后,对研磨效果影响已达到大。因此应该综合考虑到砂磨机在研磨过程中的消耗,终选择合适的研磨转速,在此例子中应该选用研磨转速到1500r/min。
七、砂磨机的温度
砂磨机对物料进行砂磨时,大约有60%~70%的转化为而损失掉。在产生大量热量时,也提高了料液的温度,同时也加剧了微粒子的布朗运动,这时会引起已被粉碎的粒子发生再凝聚现象。这时,必需要冷却料温,可以通过降冷却介质的温度,或者加大冷却剂的流量来控制料液温度。一般在加工悬浮剂时,通常控制砂磨机的温度在60℃以下是适宜的;但是对于需要加工熔点的,通常控制砂磨机的温度要更一些,有时在30℃左右。
八、结语
目前无论国内外,加工的商品化悬浮剂产品绝大多数采用湿法砂磨法,这是国内外常用和有效的方法。热熔凝聚法加工悬浮剂,虽然在实验室中是一种既简单、经济,又切实可行的加工方法,但在工业上未经实施,未必是一种简单、经济的方法。
高压均质机加工悬浮剂具有处理量大、时间短、处理次数少、占地面积少、粒径小、节省人力及降生产成本的优点,并具有10L/h至5000t/h的多种规格可以选用。特别是可以实现模块化生产,在国外已受到青睐,值得大家关注。
在研发得到悬浮剂优后,需要进行产业化,对于砂磨技术(砂磨机类型、研磨介质、研磨转速的选用和砂磨机温度控制)实施的好坏,将直接会对生产悬浮剂产品的质量产生重大影响。