行业知识
硅酸锆湿法球磨工艺中磨介的影响
作者:admin日期:2020-01-25阅读
本文对用于生产超细硅酸锆的常用研磨介质进行了分析对比,测定了其研磨损耗,研究了研磨介质的不同材质、不同粒径和粒径配比等因素对硅酸锆产品的平均粒度的影响。结果表明:市售的不同材质的研磨介质在实验条件下的损耗在0.1%~1.15%之间,均可用于湿法超细硅酸锆的生产。对于相同材质的磨介,较小直径的磨介有助于得到更细的产品,对罐体的冲击也较小。不同直径的磨介其本身磨损率相当,大小配比的效果介于大、小直径磨介之间。
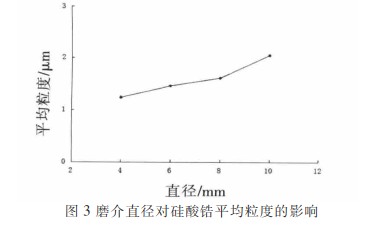
硅酸锆是指锆英砂经过超细粉磨工艺加工而成的超细粉体。我国硅酸锆的生产和应用,开始在20世纪80年代末90年代初[1]。目前,硅酸锆主要的应用是作为陶瓷乳白釉的乳浊剂,用于日用陶瓷以及建筑卫生陶瓷的釉面上[2,3]。硅酸锆产品的粒度是影响其质量的一个重要因素。
国内外的超细硅酸锆粉末的生产可以分为干法和湿法两种。湿法工艺制造是将锆英砂与水、助磨剂、研磨介质按一定比例加入球磨机,随着磨筒的转动,处于磨介之间的锆英砂受冲击、研磨和剪切等作用而被粉碎制备而成,在国内应用较多[4]。
在硅酸锆湿法生产中使用的研磨介质主要有氧化锆珠、硅酸锆珠、氧化铝球[5]。氧化锆球具有强度高、韧性好和耐磨性好的特点,并能增加超细硅酸锆产品的锆含量,其中应用较多的是钇稳定氧化锆珠。硅酸锆球以硅酸锆为原料,与超细硅酸锆产品材质相同,具有不增加杂质的优点。氧化铝球大多用α-Al2O3作原料,也有些企业采用优良、贮量丰富、价格廉的铝钒土为主要原料生产氧化铝球。氧化铝球根据氧化铝含量不同,可以分为中铝球、中高铝球和高铝球。高铝球由于其具有高强度、高硬度、高耐磨性、耐高温、耐腐蚀、无污染等优异特性,且密度大、体积小,被广泛运用于不同类型的陶瓷、瓷釉、玻璃、化工等工厂的厚硬材质精加工和深加工,其中尤以Al2O3质量分数为92%的高铝球使用为普遍[6]。
磨介的成型方法有挤压法、团球法、液压硬模成型法及等静压成型法[7],不同工艺条件下以及不同材质的研磨介质的化学成份和物理性质都不相同,研磨效果和研磨损耗也有差异。同时,研磨过程中磨损的磨介材料也对产量产生一定的影响。因此,在超细硅酸锆湿法生产中研磨介质的选取至关重要。
本文是在实验室条件下,对湿法球磨加工中的常用研磨介质进行了分析对比,测定了其研磨损耗,研究了研磨介质的不同材质、不同粒径和粒径配比等因素对硅酸锆产品的平均粒度的影响,为实际生产提供依据和指导。
2实验内容
本实验原料采用澳大利亚ILUKA公司优级锆英砂,化学成分如表1所示;研磨介质采用市售的氧化锆球、硅酸锆球和高铝球,直径为0.6~10mm;粒度测试采用欧美克LS-POP(6)型激光粒度仪;球磨机采用南京科析实验仪器研究所的XQM-2L变频行星式球磨机,球磨工艺:料浆浓度为2/3,球料比为2:1,研磨时间为10h,转速为250r/min。在上述工艺的基础上,选取不同材质、不同粒径和粒径配比的磨介进行研磨实验,然后对磨介、球罐研磨前后的质量以及所得硅酸锆的平均粒径进行测试。快速磨采用淄博雷德YMJ1型快速研磨机,转速520r/min,时间为2h,并在此条件下对不同厂家生产的不同材质的磨介的磨损进行测试。
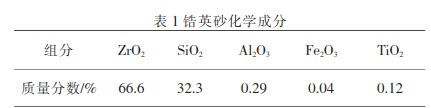
3结果与分析
本实验原料采用澳大利亚ILUKA公司优级锆英砂,化学成分如表1所示;研磨介质采用市售的氧化锆球、硅酸锆球和高铝球,直径为0.6~10mm;粒度测试采用欧美克LS-POP(6)型激光粒度仪;球磨机采用南京科析实验仪器研究所的XQM-2L变频行星式球磨机,球磨工艺:料浆浓度为2/3,球料比为2:1,研磨时间为10h,转速为250r/min。在上述工艺的基础上,选取不同材质、不同粒径和粒径配比的磨介进行研磨实验,然后对磨介、球罐研磨前后的质量以及所得硅酸锆的平均粒径进行测试。快速磨采用淄博雷德YMJ1型快速研磨机,转速520r/min,时间为2h,并在此条件下对不同厂家生产的不同材质的磨介的磨损进行测试。
3结果与分析
3.1湿法球磨工艺中不同磨介的磨损结果及分析
选取不同厂家生产的不同材质的磨介进行测试,采用快速磨,研磨时间为2h,转速520r/min,研磨介质的损耗结果如表2所示。
从表2可以看出,测试的各种磨介的磨损结果总体在0.1%~1.15%范围内,不同材质磨介的磨损结果则缺少规律性。即使同一材料的磨球,由于生产方法及工艺控制的不同,耐磨程度有较大的差别。如采用等静压成型的磨介球与注浆成型的磨介球磨耗相差很多[8]。此外,原料纯度、粒度、粉体流动性等方面的差别,也会对研磨介质的耐磨性产生影响。
3.2不同磨介材质情况下的硅酸锆平均粒度
考虑到3.1的情况,选取磨损率接近的同一直径相同
重量的三种不同材质的磨介,对锆英砂进行研磨,考察其对硅酸锆平均粒度的影响,结果如表3所示。
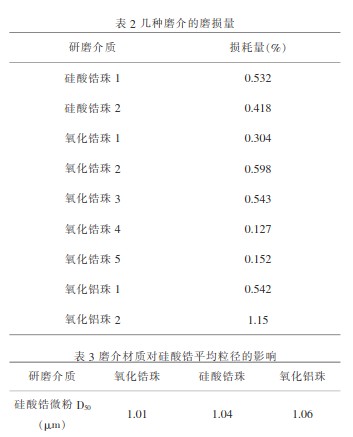
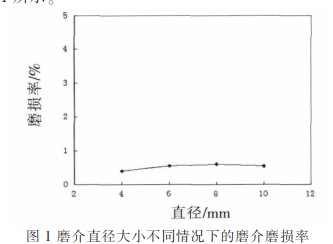
从表3可以看出,不同材质磨介得到了大致相近的结果。分析其原因,一方面,同样直径的情况下氧化锆珠拥有大的密度,硅酸锆珠次之,氧化铝珠,实测结果分别为5.36g/cm3,4.28g/cm3,3.81g/cm3。较大质量的磨介在同等运动速度的条件下拥有更高的研磨冲力,有助于得到更细的微粒,但另一方面,在同等质量的前提下,较大密度的磨介却也拥有少的单体数量,相应具有较小的比表面积以及较的冲击频率,从而可能抵消了单个球体密度较大所带来的优势。
3.3磨介直径大小不同情况下的磨介磨损结果选取同一生产厂家的直径分别为4mm、6mm、8mm、10mm的高铝球进行研磨,考察其磨损情况,结果如图1所示。
从图1可以看出,不同直径的磨介其磨损率基本保持同一数值。
3.4磨介直径大小不同情况下的罐体磨损结果
磨介直径大小不同情况下的罐体磨损结果如图2所示。
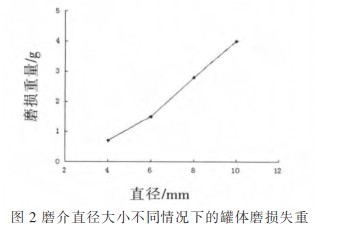
由图2可见,与球的磨损情况相比,球罐的磨损出现了随球径而逐渐的趋势。分析其原因,可能是在罐体受冲击表面大致相同的情况下,大粒径磨介球由于质量较大所造成的更强的冲击作用在球罐的磨损中扮演了主要的角色。
3.5磨介直径大小不同情况下的硅酸锆平均粒度
在3.3的实验条件下,所得的硅酸锆的平均粒度如图3所示。
由图3可见,在同样的研磨条件下,采用较小直径的磨介球得到的硅酸锆的平均粒度要小于采用较大粒度的磨介球所得到的硅酸锆的平均直径。
3.6磨介直径配比对硅酸锆平均粒度的影响
实际生产中,磨介初装时往往采用不同直径的磨介
配成一定比例加入。选取直径4mm和10mm的磨介,按重量配比(g):200:0、150:50、100:100、50:150、0:200进行测试,所得硅酸锆的平均粒度结果见图4。
由图4可见,采用不同直径磨介配比的结果介于大直径磨介和小直径磨介之间,并基本呈线性关系,并无突出优势。实际生产中,由于磨损,往往采取定期补加大直

4结论
在采用湿法球磨工艺制取硅酸锆的情况下,各类研磨介质均能用于超细硅酸锆的生产,不同厂家和材质的磨介的选择应以实际效果和成本划算为准,并结合产品的应用要求考虑。对于相同材质的磨介,较小直径的磨介有助于得到更细的产品,对罐体的冲击也较小。不同直径的磨介其本身磨损率相当,大小配比的效果介于大、小直径磨介之间。
径磨介的办法补充磨介。在初装和补加皆为单一直径磨介的情况下,由于磨介的磨损率在一定范围内随直径大小的变化不大,故球磨罐中的磨介直径在一定区间内基本是均匀分布的。
3.7磨介损耗对硅酸锆中氧化锆含量的影响
超细硅酸锆粉的加工是一种简单的物理加工过程,其化学成份理论上应和原材料化学成份一致。硅酸锆球的主要成份与锆英砂相近,对超细硅酸锆化学成份无明显影响。氧化锆球可以提高超细硅酸锆产品中氧化锆的度数,以其磨损率为0.5%,球料比2:1,原料含氧化锆66.6%计算,成品的度数大约为66.9,提高约0.3度。相反,氧化铝球的主要成份为A12O3,会引起产品中氧化锆的度数降。实际生产中,测得的结果约为降1~1.5度。当采用氧化铝球作为磨介时,如损耗过大,将影响到硅酸锆的质量和应用。
4结论
在采用湿法球磨工艺制取硅酸锆的情况下,各类研磨介质均能用于超细硅酸锆的生产,不同厂家和材质的磨介的选择应以实际效果和成本划算为准,并结合产品的应用要求考虑。对于相同材质的磨介,较小直径的磨介有助于得到更细的产品,对罐体的冲击也较小。不同直径的磨介其本身磨损率相当,大小配比的效果介于大、小直径磨介之间。