行业知识
游离粒子对摩擦电铸技术的影响
作者:admin日期:2020-08-20阅读
摩擦电铸技术是采用任何添加剂的标准电铸液,在阴阳之间添加不导电的游离粒子,在电铸过程中运动的阴带动游离粒子不断摩擦、挤压电铸层,可得到外观表面平整、光亮、无任何麻点、针眼、结瘤等缺陷的电铸层,其机械性能也非常优异。游离粒子在电铸过程中起到了至关重要的作用。选用不同直径的硅酸锆珠,作为新工艺的摩擦介质,通过对比试法来研究游离粒子的直径对电铸层表面形貌、微观组织和机械性能的影响规律。试验结果表明,在摩擦电铸过程中,游离粒子的直径对电铸层外表面质量影响非常明显。粒子直径过小,电铸工艺处于亚复合电铸状态,易造成电铸层起皮;直径太大,易导致电铸层摩擦不均匀;当粒子直径在0.4~2.0mm之间时。能获得表面光亮、平整和强度较高的电铸层。
电铸技术是一种精密特种加工方法,它是利用电化学原理在阴上进行金属电沉积,然后将金属沉积层与阴分离,以获得金属复制件的工艺过程。电铸具有很高的复制精度和重复精度。但电铸技术本身还存在着一些缺陷和局限性,如在电铸过程中,会有氢从阴表面析出,并以气泡的形式滞留
在阴表面,金属沉积,造成铸件表面出现麻点、针孔等缺陷⋯ ,使电铸层的物理、机械性能下降;由于放电效应或杂质的影响,电铸层表面易产生积瘤、应力等缺陷,造成电铸层均匀性差,整体沉积速度下降。这些问题的存在,严重了电铸工艺技术整体水平的提高及电铸技术的应用和发展。
国内外学者有关电铸的研究大都局限在电解液的上 ,而过于复杂的对于电铸来说有其不足之处。因为在电铸过程中许多添加剂会有明显消量,电解液成分会明显发生变化,从而影响电铸层的质量,电解液的维护也很困难。为了克服上述缺陷,南京航空航天大学特种加工实验室提出了一种新型的电铸技术— —摩擦电铸技术 ,即在电铸过程中利用不导电的游离粒子来摩擦电铸层表面,取得了很好的效果。本文是在此基础上,以电铸镍为例,通过改变摩擦介质的直径,进一步深入研究该技术的作用机理,探讨游离粒子在电铸过程中所发挥的作用,并通过实验的方法选择出适合此技术的粒径范围。
1 摩擦电铸的机理分析
1.1提高表面质量
1.1提高表面质量
在摩擦电铸技术中,不导电的游离粒子紧贴着阴表面,并与阴表面作相对运动。游离粒子不断摩擦阴表面,能副反应产生的氢气泡在阴表面的吸附,并将吸附在阴表面的氢气泡剥离下来进入溶液中,从而避免氢气泡滞留在电沉积层外表面或夹杂在电沉积层内而金属的沉积,达到了消除针孔、凹坑的目的,同时游离粒子还可对已形成的结瘤等微观凸起械磨削和抛光作用,从而结瘤继续长大,提高了电铸层的表面质量,如图
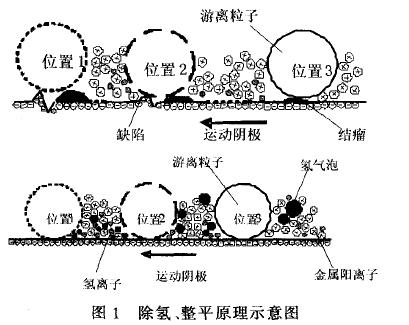
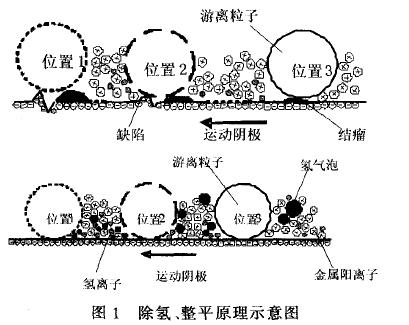
1.2 影响微观结构
在摩擦电铸技术中,不导电的游离粒子充满阴阳间的空间,电解液只是在粒子间的空隙内流动,阴和阳之间的电场通过空隙内的溶液导通。众多的粒子覆盖整个阴表面,并作复杂运动游离粒子位置不断变化,它们之间的空隙也随之变化,所以在阴表面上各部位的电场是变化的。图
2为游离粒子摩擦电沉积技术在某一瞬态的二维模型及电场分析结果。图中反映了在阴表面的各个位置均形成间断变化的电流分布,近似于脉冲电流分布,随着游离粒子位置的移动,阴表面电场分布也发生相应的变化。阴的运动速度也就是游离粒子覆盖阴表面位置的变化频率,实质上是未被游离粒子覆盖面积上电流密度的作用时间。时间的断续造成局部晶粒尚未来得及长大就被暂停了连续生长,等下一次单位面积通电时,又得从头开始形核,从而导致电铸层金属由形核到长大的完整过程被人为打断,使晶粒得到了细化;另外,游离粒子不停地摩擦阴表面,使阴表面离子放电的点增多;同时游离粒子也扰动吸附原子的扩散,改变其进入晶格的路径,增加位错露头点的数目,易得到细而多晶的电铸层。
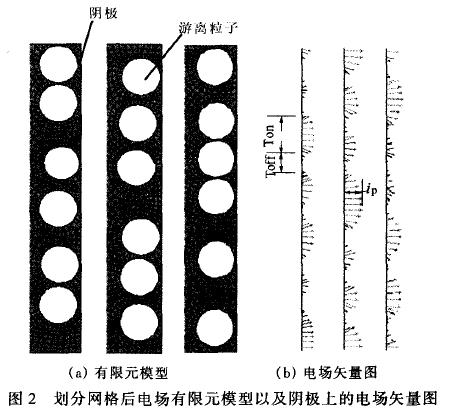
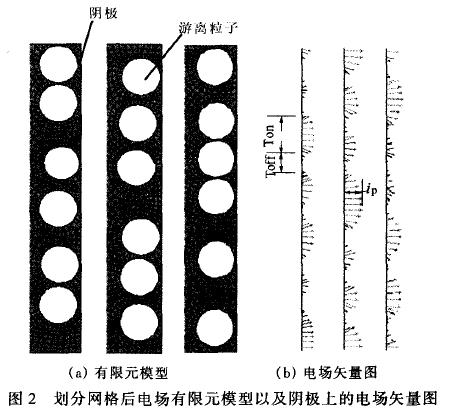
1.3 提高机械性能
采用摩擦电铸技术时,运动的游离粒子不断撞击、摩擦和挤压电铸层,能强化电铸层,使电铸层更加致密;另外,根据前面分析可知,游离粒子摩擦电铸技术能提高沉积过电位,细化晶粒。超细晶粒的存在,使单位体积内的晶界数目增多,变形抗力,这些因素都能强化电铸层,提高电铸层的机械性能。
通过对摩擦电铸技术作用机理的分析可知,此技术具有提高电铸层外表面质量、细化晶粒和提高机械性能的作用。而在新技术中,所添加的游离粒子是关键,因此有必要对游离粒子进行一定的筛选。本文将通过试验的方法研究游离粒子直径对摩擦电铸技术的影响,对游离粒子材质等方面
的影响未作考虑。主要原因是粒子的直径与其运动速度有一定的关系,而运动速度又是作用强度的一种体现。通过对比试验的方法,以游离粒子摩擦电铸技术的作用机理为判断依据,优选出适合新技术的游离粒子的直径范围,为地发挥新技术的特点提供试验和理论依据。
2 试验准备
本试验在自行研制的电铸机床上进行,其示意图见图3。调速电机带动阴在镂空的容器中运动,容器的外壁和底部均用涤纶布密封;容器和阴之间填充的硬质粒子完全覆盖阴表面;颗粒状阳围绕容器外壁放置于电铸槽内。在试验中,阳采用电镀镍珠,直径为8~12 mm,其在电铸过
程中能不断补充电铸液中镍离子的消耗。镍珠在使用前,用超声波清洗机进行清洗,然后用清水和蒸馏水洗净。采用直径不同的游离粒子(直径0~0.175mm ;0.175~ 0.25 mm ;0.4、0.6、0.8、1,2,3.5mm),运用阴旋转方式进行游离粒子摩擦电铸镍的试验。选用相同的工艺参数:电流密度4 A/din ,阴旋转速度200 r/rain,电铸液温度40℃ ,作对比试验。电铸液的成分是:氨基磺酸镍(Ni(NH ·SO,) ·4H O)400 g/I ,硼酸(H,B03)30 g/L,氯化镍(NiC1,)15 g/L。游离粒子分别经清水和蒸馏水冲洗,烘干后使用。圆柱形阴用不锈钢加工而成,沉积面积直径25 mm×40 mm。阴表面先后经抛光、除油等处理,再用蒸馏水冲洗后即刻人槽。电铸用的电源是杭州某公司生产的JC17530型直流电源。试验时,电铸层达到一定厚度后随同阴
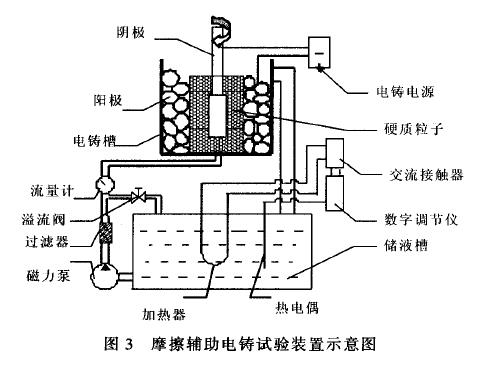
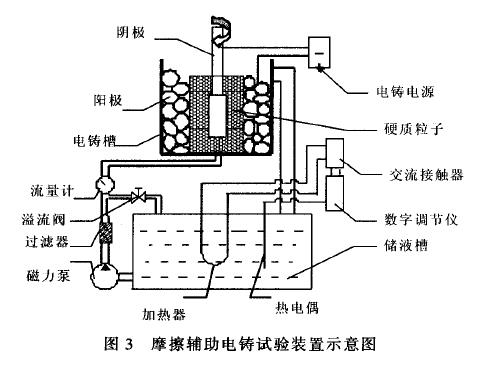
一起从夹具中取出,经清洗、干燥后进行显微硬度检测,然后用机械方法剥离,对其进行后续检测。
3 结果与分析
3.1 电铸层的表面形貌
图4分别为用不同直径游离粒子作为摩擦电铸技术的摩擦介质而制备的电铸层。从图中可看出,当游离粒子直径小于0.175 mm 时,所制备的电铸层表面起皮、开裂,呈鱼鳞状,电铸层有明显发脆现象;将电铸层剥离后,阴表面明显发黑,可断定为烧焦所致;但采用直径为0.175~0.25 mm 的游离粒子所得到的电铸层非常光亮,但仍有起皮现象,起皮的面积有所减小,电铸层仍发脆;采用直径0.4~ 2.0 mm之间的游离粒子时,得到的电铸层非常光亮,何宏观缺陷,经几次折弯后电铸层没有发生脆性断裂;当粒子直径达到3.5 nlrll时,所得到的电铸层出现条纹状痕迹,严重的甚至出现开裂现象。
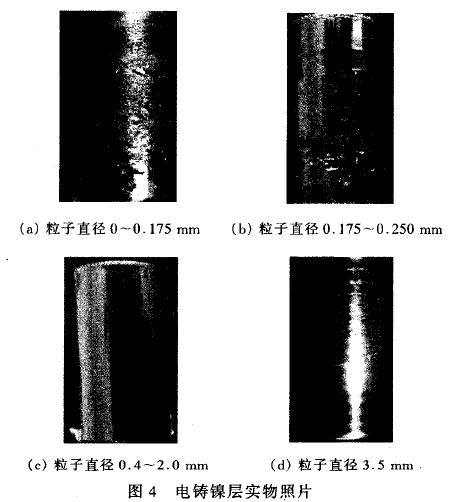
对电铸层表面形貌结果分析可知,游离粒子的直径过小时,其表面能大于自身的重力,粒子易发生团聚而结合在一起,呈泥糊状。在电铸过程中,硬质粒子不能处于游离状态,而是粘贴在阴表面,了电铸液的更新和阴表面电场的交替变化,从而导致电铸层的烧焦;当游离粒子直径过大时,由于阴阳间距以及盛放硬质粒子容器的限制,靠近阴表面的游离粒子在其他粒子的挤压等作用下,没有足够大的自由移动空间,其覆盖阴表面的位置也
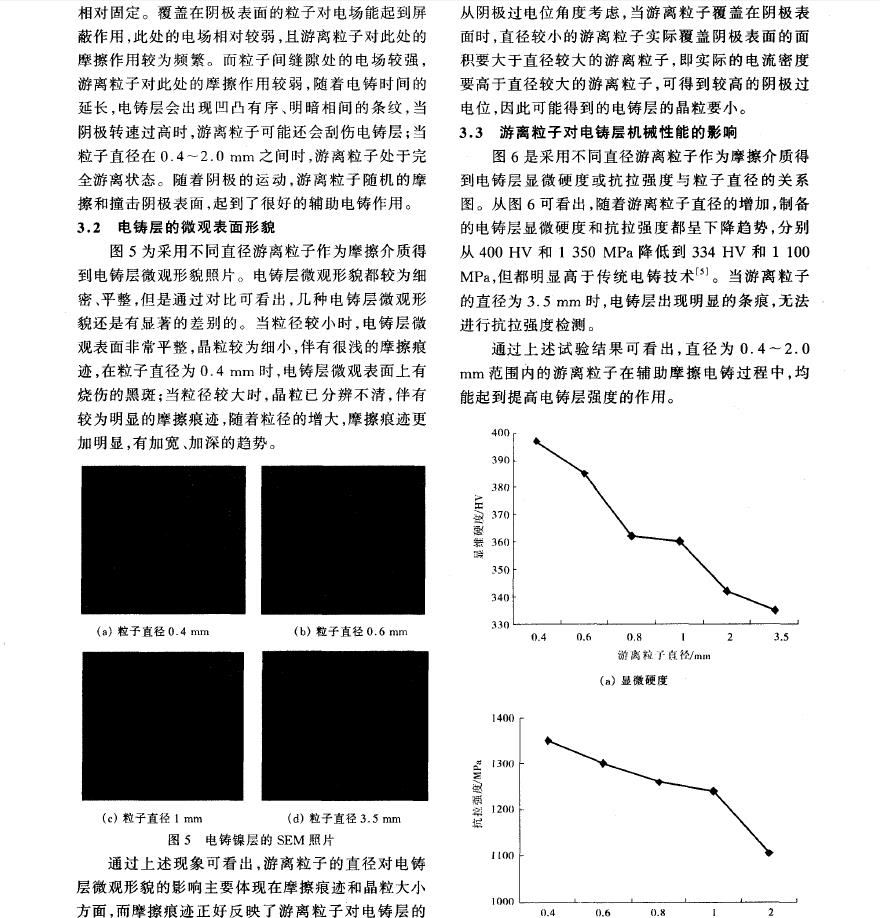

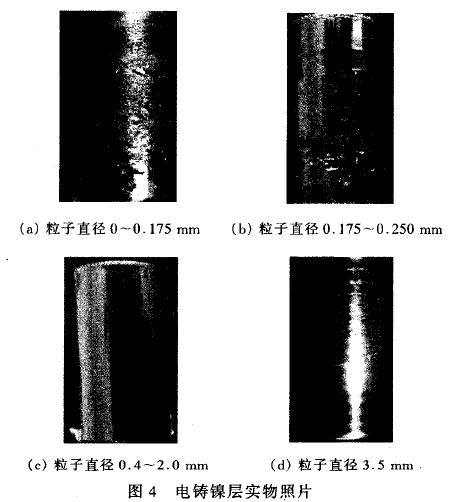
对电铸层表面形貌结果分析可知,游离粒子的直径过小时,其表面能大于自身的重力,粒子易发生团聚而结合在一起,呈泥糊状。在电铸过程中,硬质粒子不能处于游离状态,而是粘贴在阴表面,了电铸液的更新和阴表面电场的交替变化,从而导致电铸层的烧焦;当游离粒子直径过大时,由于阴阳间距以及盛放硬质粒子容器的限制,靠近阴表面的游离粒子在其他粒子的挤压等作用下,没有足够大的自由移动空间,其覆盖阴表面的位置也
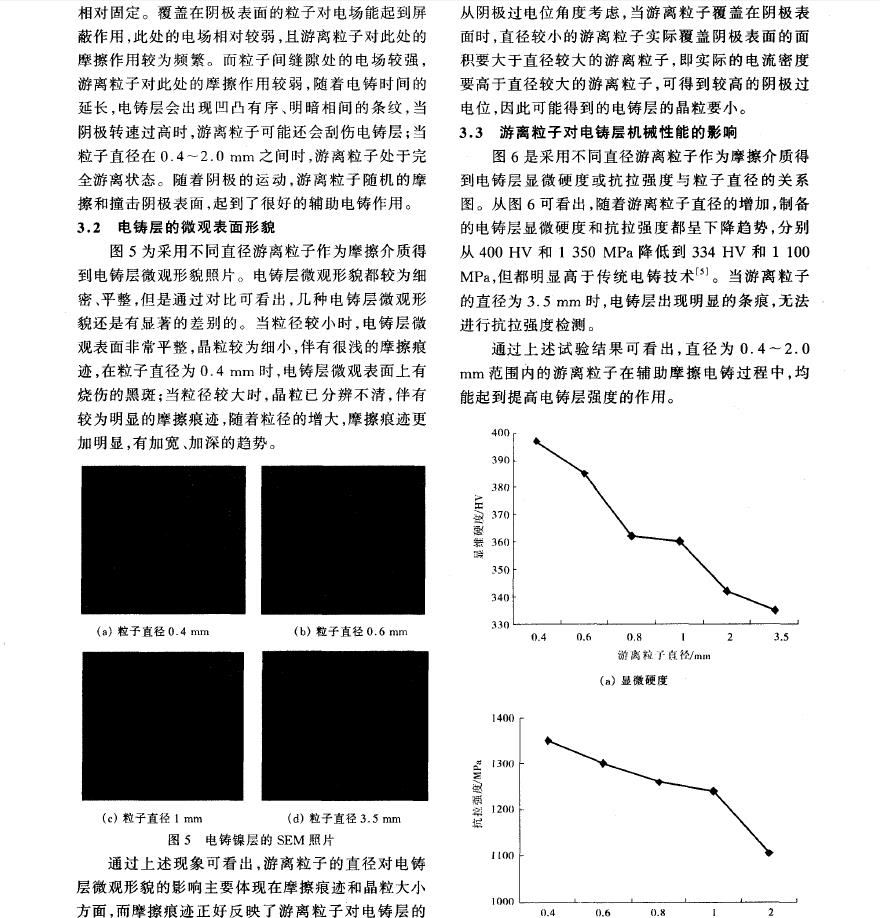

结论
通过以不同直径的游离粒子作为摩擦介质,采用相同的加工参数进行阴旋转式摩擦电铸试验,对电铸层的表面形貌、微观组织以及机械性能等方面进行了检测。以摩擦电铸技术的作用机理作为判断依据,综合比较试验结果得出,游离粒子的直径在0.4-2,0 mm之间时,均能体现摩擦电铸的特点,制备的电铸层表面光亮、平整,无任何针孔、麻点等缺陷,晶粒细小,机械性能得到了相应提高。如果粒子直径太小,电铸层表面会出现起皮、开裂等现象;如果粒子直径过大,电铸层出现条纹状痕迹,严重的甚至出现开裂现象。